引言
Ti-6Al-4V(TC4)钛合金是一种综合性能优异的材料,其密度较小,且具有优异的比强度、比刚度,良好的耐腐蚀和耐高温性能,因此被广泛应用于航空、航天和航海领域的关键结构零件中,例如,航空发动机的压气机叶片等[1-3]。但是,随着我国飞机在海上执行任务越来越频繁,受潮湿海洋大气等因素的影响,机体部件易发生电化学腐烛。同时,部件表面在运行过程中易受外物损伤,从而导致失效[4-5]。
因此,材料表面硬度与耐腐蚀性能的提高对关键部件使用可靠性的提高和使用寿命延长具有重要意义。
激光冲击强化(LSP)是一种新兴的金属材料表面处理技术,通过高应变率表面冲击处理来提高金属材料的表面硬度、耐腐蚀性能和疲劳寿命[6-7]。目前,国内外学者在激光冲击强化提高金属材料的表面性能和疲劳寿命等方面已有了一些研究。王江涛等[8]发现,激光冲击强化可以使7075铝合金焊接头处的晶粒得到高度细化,降低显微孔洞和气穴数量,有效地阻止了溶液中的离子渗入,从而降低了腐蚀速率。Yang等[9]对冲击强化后异物损伤TC4的疲劳行为进行了研究。发现LSP可以通过诱导产生 高残余压应力来降低疲劳裂纹的增长速度。Tong等[10]的研究结果显示,无吸收层激光冲击强化(LSPwC)可以使AA5083铝合金的抗空蚀能力提 高2.13倍。近年来,一些人开始研究对增材制造件进行激光冲击强化。Jin等[11-12]研究发现,激光冲击强化后,增材制造的TC4试样表面硬度增加了约11%。Yeo等[13]的研究表明,激光冲击强化可以使TC4钛合金增材制造件的冲击韧性提高120%。赖梦琪等[14]则发现激光冲击强化可以提高TC4增材
件的致密度。宋亚杰等[15]研究结果显示,经过3次激光冲击强化后,激光增材的GH1131合金薄壁件的表面硬度提高了66.6%。上述研究表明,激光冲击强化可以有效提高金属材料的耐腐蚀性能、表面硬度、冲击韧性等,并降低裂纹的扩展速度。但单独的激光冲击强化技术对于材料性能的提升具有一定上限。为了满足航空航天零件恶劣的工作环境需求,需要将激光冲击强化工艺与其他的工艺进行复合,进一步提升对材料的强化效果。Jia等[16]研究了激光冲击强化和热处理对电子束焊接Ti-6.5A-1Mo-1V-2Zr的微观硬度、拉伸性能和微观结构的影响,发现冲击强化后热处理的试样的最大抗拉强度相比单独热处理试样和原始试样都有所增加。
Ren等[17]研究了激光冲击强化和热处理温度对AZ91D镁合金显微组织的影响,发现冲击强化后适当温度的热处理可以使晶粒尺寸进一步减小。其中 当退火温度为200℃时表面纳米晶的尺寸最小,约为50nm。Kalentics等[18]则将增材制造、激光冲击强化和热处理进行了结合,结果显示,增材制造的 CM247LC合金试样进行冲击强化后再热处理,其裂纹数量下降了95%。
已有研究表明,对激光冲击强化后的试样进行热处理可以得到综合性能较为优异的材料,然而此复合工艺对于TC4钛合金耐腐蚀性能和表面硬度的研究尚未报道,有待研究。因此,本文对与航空发动机叶片相同工艺条件的TC4钛合金锻件进行激光冲击强化与热处理复合处理,分别对材料进行1、2次激光冲击强化,并对冲击强化后的材料进行了热处理,研究了激光冲击强化和热处理复合工艺对TC4材料微观形貌、表面硬度与耐腐蚀性能的影响,分析并总结了其影响规律。
1、试验材料和试验方法
1.1试验材料
试验材料为7mm厚的Ti-6Al-4V(TC4)锻件,其化学成分如表1所示。所有的试样通过线切割加工制备成尺寸为200mm×200mm×7mm的方形块体,然后用酒精清洗干净。

1.2试验方法
激光冲击强化所使用的激光器为Nd:YAG激光器,其输出能量为2.8J,波长为532nm、脉冲频率为1Hz,脉冲宽度为14ns。在激光冲击强化过程中,所选用的光斑直径为2mm,光斑搭接率为50%,激光功率密度为6.37GW/cm2。同时,使用1mm的水层和厚度为0.12mm的黑色电工绝缘胶带作为激光冲击强化的约束层和吸收层。激光冲击强化的原理与路径如图1所示。将部分激光冲击强化后的试样进行热处理。试样的热处理是在真空气氛炉(SQFL-1400)中进行的。将试样在1h内加热到600℃,并在600℃下保持1h,然后进行炉冷。将进行0、1、2次冲击强化后的试样分别记为0、L-1、L-2,将冲击1次和2次后进行热处理的试样分别命名为L-1-O和L-2-O。具体的工艺参数见表2。
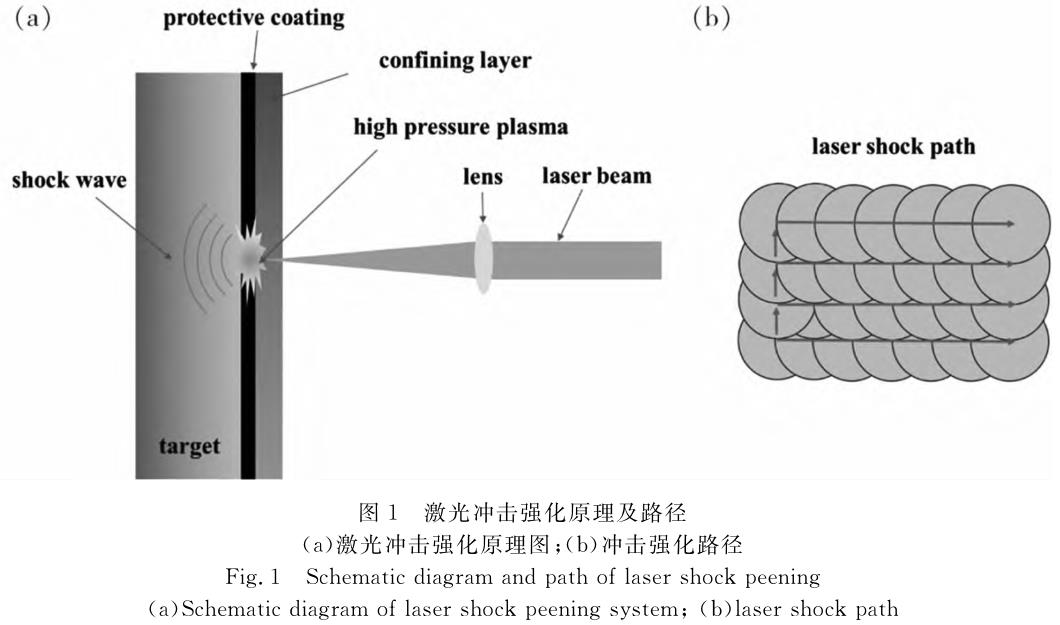

通过激光共聚焦显微镜(VK-X100K/X200K)对试件表面形貌进行观测,测量其表面粗糙度。为了观察横截面的微观结构,对试样的横截面用60~1500#的砂纸进行研磨,然后进行抛光。每个试样都使用扫描电子显微镜(SEM,FEIQuantaFEG250)和电子背散射衍射(EBSD)进行观察。利用 RDHVS-1000Z维氏硬度计测量试样的表面硬度,测量载荷为25g,保荷时间为10s。利用线切割将各个试样截取规格为6×6×7mm3的方形块体,将试样用无水乙醇进行清洗,最后利用超声波进行清洗,并冷风吹干。电化学腐蚀采用武汉科思特仪器公司的CS系列电化学工作站进行测量。采用三电极体系,辅助电极为铂电极,参比电极为Ag/AgCl(饱和KCl)电极,电解质为质量分数3.5%的NaCl溶液,试样工作面积为0.0126cm2。极化曲线试验以动电位扫描法测定试样的自腐蚀电位和腐蚀电流密度,并根据Tafel外推法计算试样的腐蚀速率,试验采用的扫描速率为1mV/s。
2、结果与讨论
2.1表面形貌
各个试样的表面形貌如图2所示。可以看出,激光冲击强化所产生的冲击波在材料表面产生了塑性变形,并出现凹、凸的形貌。通过测试得知,0、L-1、L-2、L-1-O和L-2-O试样的表面粗糙度分别为1.63μm、1.94μm、2.14μm、1.77μm和2.14μm。
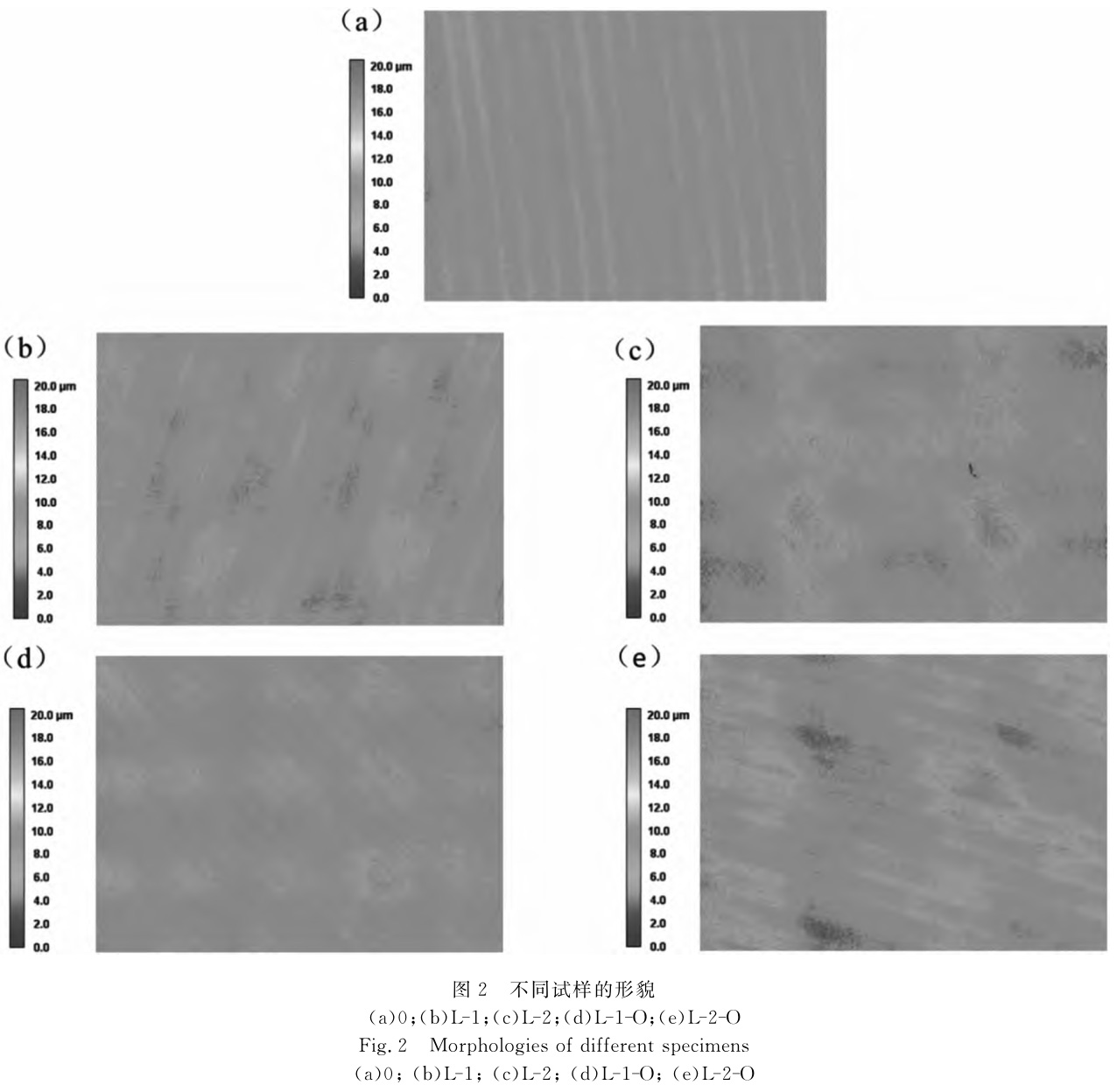
激光冲击强化后,材料的表面发生了塑性变形[19],从而导致了其表面粗糙度的增大,且L-2表面的粗糙度大于L-1处理表面的粗糙度。而热处理之后,试样在600℃下可能发生了再结晶[20],所以试样的表面粗糙度相比冲击强化的试样有所下降或者不变,但仍较原始试样的表面粗糙度高。
2.2微观结构
图3和图4分别是原始试样和处理后试样的截面形貌SEM图像和晶界分布图。如图3(a)和图3(b)所示,可以发现原始试样的α相晶粒较大,β相的分布也比较聚集。对比图3(a)和图4(a),冲击强化后,L-1试样的β相变得更加细长,且多分布在α相的周围,不再出现大量聚集的组织形貌。同时,靠近冲击面的晶粒在冲击强化后发生了明显的变形。
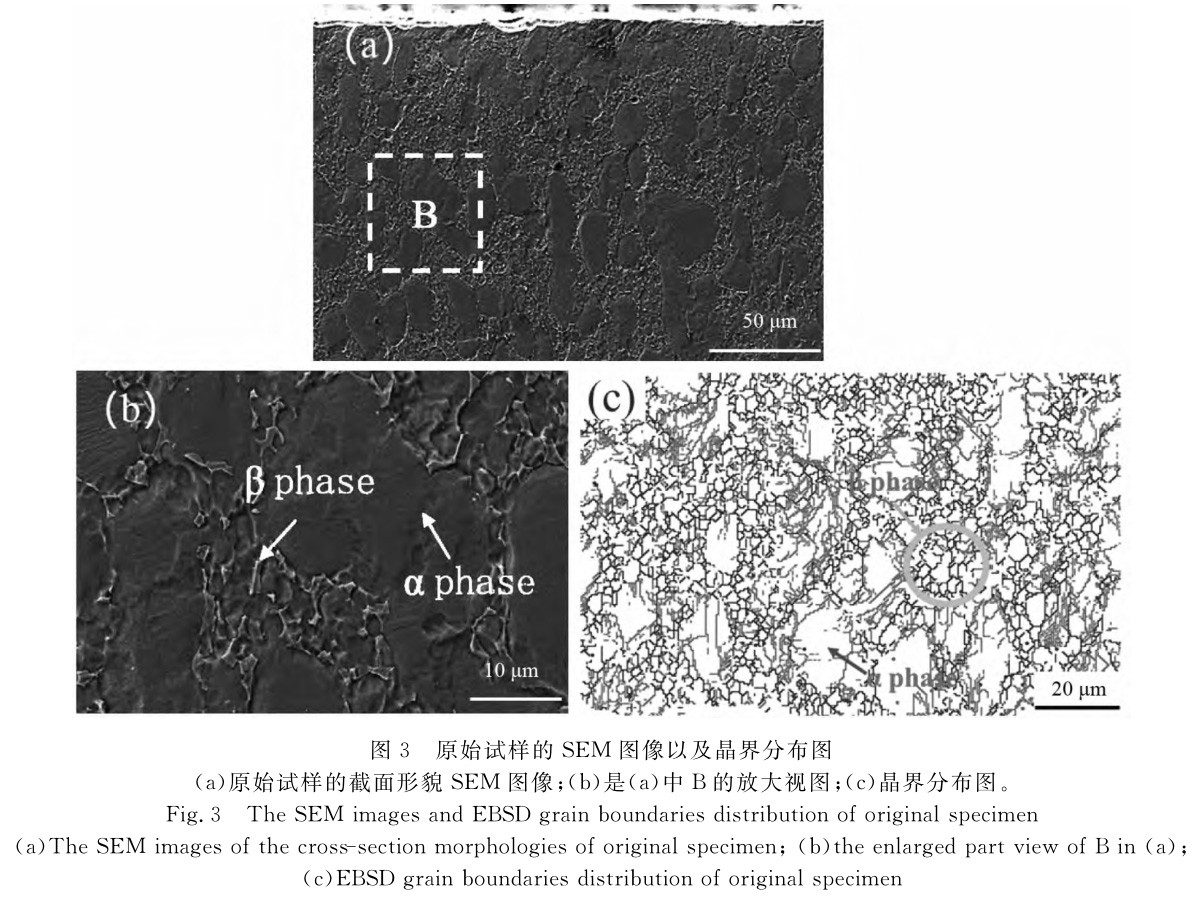
图4(b)显示了L-2试样的α相晶粒尺寸相比原始试样和L-1试样要更加细小。从图4(f)中的黄色框内可以看到,α相晶粒内部出现了一些形变界面,这可能是由于多次冲击强化所产生的冲击波使得晶粒内部发生了变形。对于L-1-O试样,与L-1试样相比,热处理后试样的β相的分布再次集中,同时靠近冲击面的晶粒发生的变形未明显改变。如图4(h)所示,L-2-O试样相比L-2试样,在热处理后其α相晶粒内部的形变界面消失。
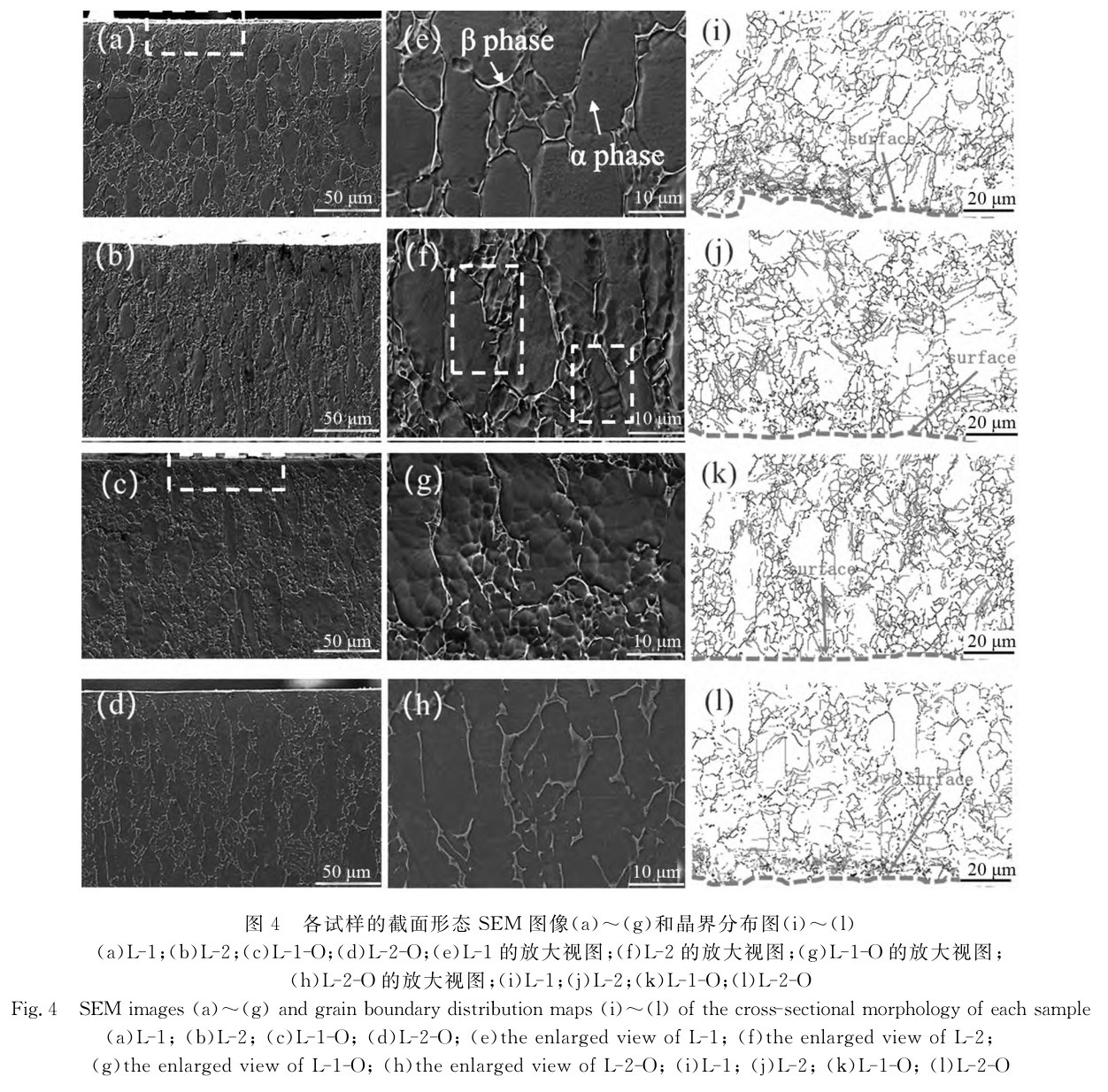
当相邻晶粒的取向差Δρ<15°时,称之为小角度晶界,取向差Δρ>15°时则称之为大角度晶界。在晶粒细化的过程中,塑性变形会引起高密度位错、孪晶等微观形貌的变化,在晶粒内部逐渐形成小角度的亚晶界,进一步演化后会发展成大角度晶界,大角度晶界会产生切割效应,将整个晶粒形成具有取向性的细小晶粒,实现晶粒细化[21]。图3和图4中的红色晶界为小角度晶界,黑色的为大角度晶界。
α相和β相是两种不同的相,因此α相和β相之间的晶界都是大角度晶界。将图3(a)与图3(b)和图3(c)进行对比,可以看到大角度的晶界的分布与β相的分布位置是比较吻合的,同时可以看出小角度晶界绝大多数都分布在α相内[21]。对比图3(c)和图4(i),可以看出试样在经过冲击强化后,大角度晶界的聚集减少,这与L-1试样在一次冲击强化后,β相的分布开始分散的情况是吻合的。如图4(j)所示,L-2相比L-1内部大角度晶界增多,表面小角度晶界减少。从图4(i)和图4(k)可见,热处理后L-1-O表面小角度晶界减少,内部小角度晶界增多,且变得集中。而从图4(l)中可以看出,L-2-O相比L-2表面大角度晶界减少,小角度晶界增多。可能是热处理之后,大角度晶界转变成了小角度晶界。这些结果都与SEM的结果相吻合。而L-2-O与相比L-1-O,其表面的小角度晶界仍然较多,说明两次冲击后的材料保持其强化后的形态的能力更强。
2.3表面硬度
从图5中可以看出,原始试样的表面硬度约为378.6HV,而L-1和L-2的表面硬度约为425.4HV和456.5HV,分别比原始试样高12.3%和20.5%。
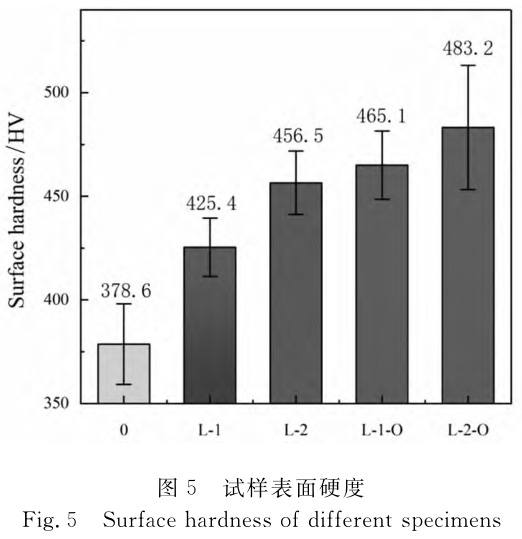
随着冲击强化次数的增加,材料的表面硬度也随之增加。材料表面硬度的提高主要归因于激光冲击强化引起的塑性变形和晶粒细化。热处理后,L-1-O的表面硬度约为465.1HV,相比L-1增加了9.3%,而L-2-O的表面硬度约为483.2HV,相比L-2增加了5.8%,比原始试样的表面硬度提高了27.6%。与只经过冲击强化处理的TC4试样相比,硬度也有提高。这表明激光冲击强化和热处理的结合工艺可以进一步提高TC4的表面硬度。
2.4动电位极化曲线
不同试样在质量分数为3.5%NaCl溶液中的动电位电位极化曲线如图6所示。从中可以看出,各试样的动电位极化曲线形状相差不大,均存在钝化区。通过图6根据塔菲尔外推法计算出不同试样的腐蚀电位和腐蚀电流密度如表3所示。
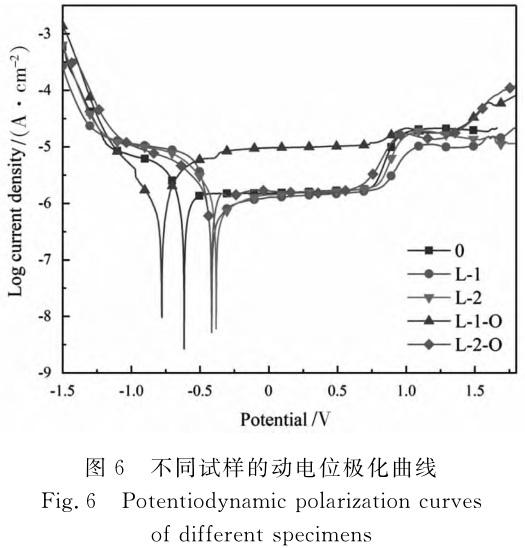
从图6及表3可以看出,原始试样的自腐蚀电位为-0.61595V,而经过一次和两次激光冲击强化的试样的自腐蚀电位分别为-0.41510V和-0.38204V。冲击强化后试样的自腐蚀电位相比原始试样发生了正移,而且随着激光冲击次数的增加,TC4钛合金自腐蚀电位逐渐正移。表明随着激光冲击次数的增加,在电化学腐蚀过程中,冲击强化后的表面层更容易发生钝化,耐腐蚀性能更佳,更不易发生腐蚀[22]。经过冲击强化后,试样的耐腐蚀性能得到提升的原因可能是冲击强化后试样表面的大角度晶界增多,大角度晶界更不易被腐蚀,因此经过两次冲击强化后的试样的耐腐蚀性能更好。
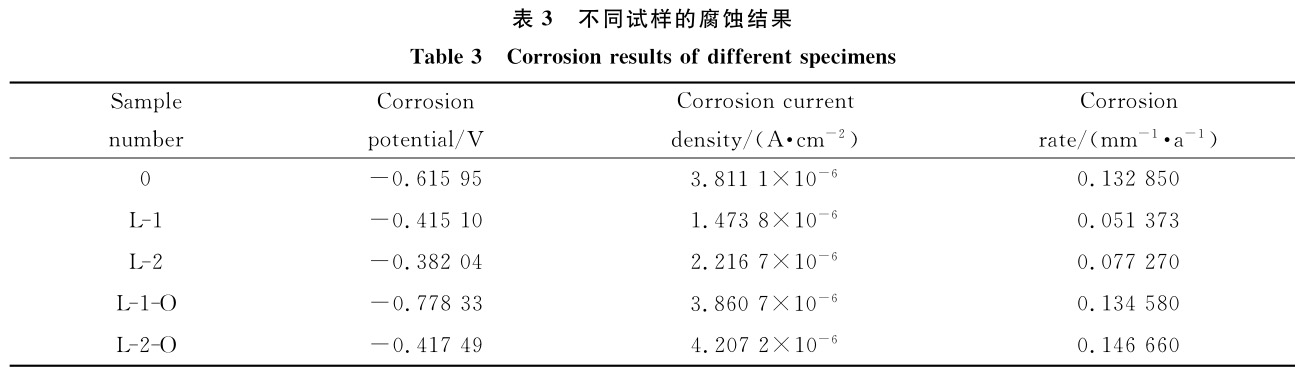
与此同时,0、L-1和L-2的自腐蚀电流密度分别为3.8111μA/cm2、1.4738μA/cm2和2.2167μA/cm2。
经过冲击强化后,试样的腐蚀电流密度减小,说明当试样发生腐蚀后,其腐蚀速率降低,耐腐蚀性能得到了提升。L-1和L-2的腐蚀速率相比原始试样分别降低了61.3%和41.8%。L-2的腐蚀电流密度相比L-1有所上升,原因可能是激光冲击强化次数增多后,试样表面粗糙度增大,使得腐蚀接触面积增大,进而导致腐蚀电流密度的上升。这表明L-2试样相比L-1试样受腐蚀的倾向更小,但其一旦受到腐蚀,其腐蚀速率将大于L-1试样[23]。
热处理之后,L-1-O的自腐蚀电位相比L-1向负移动了0.36323V,其腐蚀电流密度相比L-1则提高了1.6倍。而L-2-O的自腐蚀电位相比L-2向负移动了0.03545V,其腐蚀电流密度相比L-2则提高了89.8%。说明了热处理后,试样的腐蚀速率提高,耐腐蚀性能下降。可能是由于热处理之后,试样表面的晶粒变大所导致的。L-2-O的自腐蚀电位相比L-1-O向正方向移动了0.36084V,说明其更不易发生电化学腐蚀,这可能与其表面小角度晶界较多有关。L-1-O和L-2-O试样的自腐蚀电流密度和腐蚀速率与原始试样相比未发生明显变化,说明TC4试样在经过激光冲击强化与热处理复合工艺处理后,其耐腐蚀性能与未处理前基本保持一致。
3、结论
(1)激光冲击强化后,TC4试样表面粗糙度增大,且试样表面的粗糙度会随着激光冲击强化次数的增加而变大。而热处理之后,试样的表面粗糙度有所下降。激光冲击强化后,β相均匀地分布在α相周围。同时,靠近冲击面的晶粒发生了明显的变形,并且在α相晶粒内部也出现了一些变形界面。热处理后试样的形变界面消失了,α相晶粒尺寸增大,β相的分布再次集中,同时靠近冲击面的晶粒发生的变形并未明显改变。
(2)随着冲击强化次数的增加,材料表面硬度也在提高。L-1和L-2试样表面硬度相比原始试样分别提高了12.3%和20.5%。热处理后,L-1-O的表面硬度相比L-1增加了9.3%,而L-2-O的表面硬度达到了483.2HV,相比原始试样提高了27.6%。激光冲击强化和热处理的结合可以进一步提高TC4的表面硬度。
(3)激光冲击强化后TC4试样的自腐蚀电位发生了正移,腐蚀电流密度下降。L-1和L-2的腐蚀速率相比原始试样分别降低了61.3%和41.8%。激光冲击强化后,腐蚀速率变缓,耐腐蚀性能提升。热处理之后,TC4试样自腐蚀电位向负移动,其腐蚀电流密度上升。表明热处理后,试样的腐蚀速率提高,耐腐蚀性能下降。TC4试样在经过激光冲击强化与热处理复合工艺处理后,其耐腐蚀性能与未处理前基本保持一致。激光冲击强化与热处理复合工艺在保持原有耐腐蚀性能的同时,可以有效提高TC4的表面硬度。
参考文献
[1]刘庆瑔.航空发动机钛合金叶片制造技术及失效分析[M].北京:航空工业出版社,2018:10-32.
LIUQQ.Manufacturingtechnologyandfailureanalysisoftitaniumalloybladesforaero-engine[M].Beijing:AviationIndustryPress,2018:10-32.
[2]尚进,曹玮,陈永畅.超声冲击结合电火花沉积的表面处理对TC4钛合金耐蚀性的影响[J].腐蚀与防护,2021,42(5):22-25.
SHANGJ,CAOW,CHENYC.Effectofsurface-treatmentofultrasounicimpactcombinedwithelectro-sparkdepositiononcorrosionresistanceofTC4titaniumalloy[J].CorrosionandProtection,2021,42(5):22-25.
[3]廖聪豪,周静,沈洪.增材制造TC4钛合金在激光抛光前后的电化学腐蚀性能[J].中国激光,2020,47(1):0102003.
LIAOCH,ZHOUJ,SHENH.Electrochemicalcorro-sionbehaviorsbeforeandafterlaserpolishingofadditivemanufacturedTC4titaniumalloy[J].ChineseJournalofLasers,2020,47(1):0102003.
[4]霍武军,孙护国.海航发动机压气机叶片腐蚀与防护措施[J].航空工程与维修,2002(6):39-41.
HUOWJ,SUNHG.Corrosionandprecautionforbladesofaero-enginecompressorinthenavyairarm[J].AviationEngineerging&Mainienance,2002(6):39-41.
[5]余钟芬.高低温交互作用下镍基高温合金腐蚀行为的研究[D].沈阳:东北大学,2014.
YUZF.Studyoncorrosionbehaviorofnickel-basedsu-peralloyunderhigh-lowtemperatureinteraction[D].Shenyang:NortheasternUniversity,2014.
[6]黄潇,曹子文,常明,等.激光冲击强化对TC4钛合金单面修饰激光焊接接头疲劳性能的影响[J].中国机械工程,2018,29(1):104-109.
HUANGX,CAOZW,CHANGM,etal.EffectsoflasershockprocessingonfatigueperformancesofTC4titaniumalloysingle-sidelasermodificationweldingjoints[J].ChinaMechanicalEngineering,2018,29(1):104-109.
[7]李松柏,张程,李湘,等.激光冲击强化对2524铝合金疲劳寿命的影响[J].表面技术,2020,49(5):207-213.
LISB,ZHANGC,LIX,etal.Effectoflasershockpeeningonfatiguelifeof2524aluminumalloy[J].Sur-facetechnology,2020,49(5):204-213.
[8]王江涛,张永康,陈菊芳,等.强激光冲击对7075铝合金等离子弧焊接头电化学腐蚀行为的影响[J].中国激光,2015,42(12):1203006.
WANGJT,ZHANGYK,CHENJF,etal.Effectofla-sershockprocessingonelectrochemicalcorrosionbehaviorof7075aluminumalloyplasmaarcweldments[J].ChineseJournalofLasers,2015,42(12):1203006.
[9]YANGY,ZHOUWF,CHENBQ,etal.FatiguebehaviorsofforeignobjectdamagedTi-6Al-4Valloysunderlasershockpeening[J].InternationalJournalofFatigue,2020,136:105596.
[10]TONGZP,JIAOJF,ZHOUWF,etal.ImprovementincavitationerosionresistanceofAA5083aluminiumalloybylasershockprocessing[J].SurfaceandCoatingsTech-nology,2019,377:124799.
[11]JINXY,LANL,GAOS,etal.EffectsoflasershockpeeningonmicrostructureandfatiguebehaviorofTi-6Al-4Valloyfabricatedviaelectronbeammelting[J].MaterialsScienceandEngineering:A,2020,780:139199.
[12]LANL,JINXY,GAOS,etal.Microstructuralevo-lutionandstressstaterelatedtomechanicalpropertiesofelectronbeammeltedTi-6Al-4Valloymodifiedbylasershockpeening[J].JournalofMaterialsScience&Technology,2020,50:153-161.
[13]YEOI,BAES,AMANOVA,etal.Effectoflasershockpeeningonpropertiesofheat-treatedTi-6Al-4Vmanufacturedbylaserpowderbedfusion[J].Interna-tionalJournalofPrecisionEngineeringandManufac-turing-GreenTechnology,2021,8(4):1137-1150.
[14]赖梦琪,胡宗浩,胡永祥,等.增材制造钛合金激光喷丸强化表面完整性影响实验研究[J].应用激光,2019,39(1):9-16.
LAIMQ,HUZH,HUYX,etal.Effectoflaserpeeningonsurfaceintegrityofadditivemanufacturedtitaniumalloy[J].AppliedLaser,2019,39(1):9-16.
[15]宋亚杰,张胜泉,吴东.激光冲击强化对激光增材GH1131合金薄壁件表面完整性的影响[J].应用激光,2020,40(3):447-453.
SONGYJ,ZHANGSQ,WUD.Effectoflasershockpeeingonsurfaceintegrityoflaseradditivemanu-facturedGH1131alloythin-walledcomponents[J].AppliedLaser,2020,40(3):447-453.
[16]JIAWJ,ZHAOHZ,ZANYX,etal.Effectofheattreatmentandlasershockpeeningonthemicrostruc-turesandpropertiesofelectronbeamweldedTi-6.5Al-1Mo-1V-2Zrjoints[J].Vacuum,2018,155:496-503.
[17]RENXD,YANGXQ,ZHOUWF,etal.Thermalstabilityofsurfacenano-crystallizationlayerinAZ91Dmagnesiumalloyinducedbylasershockpeening[J].SurfaceandCoatingsTechnology,2018,334:182-188.
[18]KALENTICSN,SOHRABIN,TABASIHG,etal.Healingcracksinselectivelasermeltingby3Dlasershockpeening[J].AdditiveManufacturing,2019,30:100881.
[19]宁成义,黄亿辉,张广义,等.激光冲击强化6061铝合金的耐磨性能及电化学性能[J].激光与光电子学进展,2018,55(6):061403.
NINGCY,HUANGYH,ZHANGGY,etal.Wearresistanceandelectrochemicalpropertiesof6061alumi-numalloystreatedbylasershockpeening[J].Laser&OptoelectronicsProgress,2018,55(6):061403.
[20]PANXL,WANGXD,TIANZ,etal.EffectofdynamicrecrystallizationontextureorientationandgrainrefinementofTi6Al4Vtitaniumalloysubjectedtolasershockpeening[J].JournalofAlloysandCom-pounds,2021,850:156672.
[21]徐松超,盖鹏涛,付雪松,等.干、湿喷丸强化对TC17钛合金喷丸强化层的影响[J].表面技术,2021,50(9):91-98.
XUSC,GAIPT,FUXS,etal.InfluencesofdryandwetshotpeeningprocessonstrengtheninglayerofTC17titaniumalloy[J].SurfaceTechnology,2021,50(9):91-98.
[22]宗洧安.生物医用钛合金增材制造成形工艺及性能研究[D].沈阳:沈阳工业大学,2020.
ZONGWA.Studyonmanufacturingprocessandprop-ertiesofbiomedicaltitaniumalloyadditive[D].Sheny-ang:ShenyangUniversityofTechnology,2020.
[23]王进,余国庆,王国迪,等.退火温度对MAO-TC4钛合金表面组织及腐蚀性能的影响[J].金属热处理,2021,46(6):65-69.
WANGJ,YUGQ,WANGGD,etal.Effectofan-nealingtemperatureonsurfacemicrostructureandcor-rosionpropertiesofMAO-TC4titaniumalloy[J].HeatTreatmentofMetals,2021,46(6):65-69.
相关链接