纯钛一般是指纯度( 质量分数) 大于99%的钛及钛合金材料, 其中高纯钛纯度可以达到4N级( 99.99%) , 甚至更高。作为钛系列产品中的一员, 高纯钛除具有密度低、熔点高、抗腐蚀性强等性质外, 还具有强度低、塑性好( 延伸率可达50%~60%, 断面收缩率可达70%~80%) 等特点。近年来, 随着航空航天、电子信息等高科技产业的快速发展, 高纯钛的用量也越来越多, 采用适当的方法制造高品质、低成本的高纯钛, 关系到这些行业的发展。
高纯钛的生产方法
高纯钛的制备方法可以分为物理法和化学精炼法两大类。其中物理法主要有区域熔炼法、偏析法、高真空熔炼法、真空蒸馏法、电迁移法、电磁场提纯法、光激发精制法、电子束熔炼法等。
化学精炼法主要有溶剂萃取法、置换沉淀法、氯化物精馏法、碘化物热分解法、歧化分解法、熔析精炼法、熔盐电解法等。在上述方法中, 得到广泛应用和发展的有克劳尔法、碘化物热分解法、熔盐电解精炼法和电子束熔炼法。一般而言, 克劳尔法的纯度可达4N~5N 级, 电解法和碘化法的纯度可达5N~6N( 气体元素除外)级, 此外, 几种精炼方法的结合可以进一步提高钛的纯度, 可以达到7N级。
1、 克劳尔法
1.1 基本原理
克劳尔法是国内外批量生产海绵钛的主要方法, 其还原反应如( 1) 式所示。
TiCl4+2Mg( l) →Ti( s) +2MgCl2 ( l) ( 1)
克劳尔法生产海绵钛的具体工艺流程为: 首先是要进行选矿, 然后将钛矿在石油焦和氯气的作用下制得到粗TiCl4, 粗TiCl4 再经过蒸馏除杂和反应除钒后得精制TiCl4, 精制TiCl4 加入到盛有熔融Mg 液的特定反应容器中进行还原, 反应结束后蒸馏除去过剩的Mg 和MgCl2, 得到海绵状的钛坨,最后取出钛坨经过粉碎、分级、封装等得到商品海绵钛。
1.2 提高钛纯度的新进展
根据海绵钛的硬度和杂质含量, 可将海绵钛分为6个级别, 其中零级海绵钛纯度为99.7%。国内还没有采用Kroll 法直接生产高纯钛的有关报道。
日本自1987 年住友钛公司就采用克劳尔法生产出了3N8 级海绵钛( 不包括气体元素含量) 以来, 经过多年的技术革新, 2001 年已经能够生产出5N
( 99.999%) 级高纯钛。表1 是列出了日本采用克劳尔法制备的不同级别高纯钛的杂质含量。
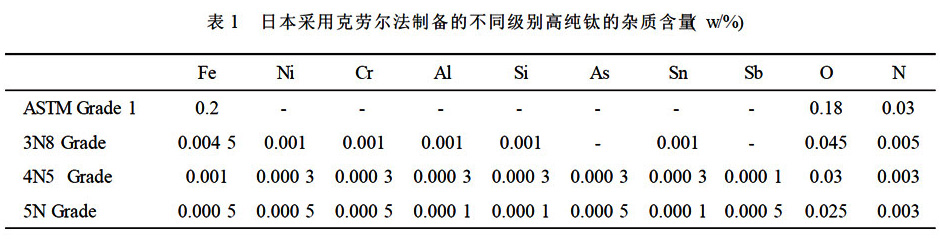
为了提高海绵钛的品质, 日本东邦钛和住友钛两大公司从原料、设备和工艺等方面进行革新, 值得我们借鉴。
原料方面必须首先提高TiCl4 和Mg 的纯度, 因为海绵钛中一半以上的杂质来源于原材料, 生产5N级钛时TiCl4 纯度要达到6N 级。为此, 日本东邦钛公司改进了TiCl4 的精馏工艺, 使得TiCl4 杂质元素含量极低, 其中As, Sb, Sn 的含量由原来的0.001%,0.000 2%, 0.000 3%下降到0.000 001%, 0.000 007%,0.000 001%( 质量百分数) 。在提高TiCl4 纯度的同时, 必须减少MgCl2 电解和Mg 运输过程中金属元素对Mg 的污染。为此, 日本采用纯铁制作盛Mg装置, 减少了镍的污染。在电解过程中, 采用静置和废钛过滤法除去MgCl2 中的Ni, 然后精练, 使得海绵钛生产中Ni 的质量百分数由0.003%~0.03%降到0.000 2%以下。
还原蒸馏容器是造成海绵钛污染的主要根源,尤其是重金属元素Fe, Cr, Ni 的污染。为了降低这些元素的污染, 近年来国内外均采取了一系列措施。日本东邦钛公司新开发出了一种不锈钢代替SUS316 和SUS321 不锈钢制造反应容器, 取得了较好效果。此外还采用铬镍含量极低的软钢作为还原蒸馏容器的内衬材料, 减少重金属元素的污染,但是制造此类容器成本有很大提高。近年来, 弁理士、柳館隆彦等研究人员认为, 还原蒸馏容器和筛板残留的海绵钛会对再生产有很大影响, 尤其是筛板的影响。采用物理方法清除残余海绵钛有利用
提高高纯海绵钛的收率。对还原蒸馏容器进行化学处理, 防止器壁与TiCl4 的反应以及物理扩散的作用也可以减少海绵钛的污染。日本有专利认为,遮热板是Fe 杂质的重要来源, 采用TiO2, SiO2,Al2O3 涂层, 可以有效防止TiCl4 和容器器壁的反应, 从而大大减少Fe 的污染, 使铁的质量百分数降低到0.003%。虽然国内也有专利对渗钛工艺进行了改进, 但实用性还有待研究。工艺改进方面, 除了传统方式, 如均匀加料、减少容器的漏气等, 日本还提出以下几个新观点值得思考: ① 采用空气- 雾化水法降低还原期间的反应温度, 从而提高加料速度, 降低Fe 含量; ② 采取相应的措施使钛坨中心温度达到炉温的均温区温度, 最大限度的除去残留MgCl2; ③ 革新蒸馏工艺, 实现蒸馏自动化; ④ 改善破碎工艺, 提高钛坨中心高纯钛的收率。
2、碘化法
2.1 基本原理
碘化法利用碘几乎不溶于钛, 但能够与钛反应的原理提纯钛。早在1925 年, 碘化法就已经提出,它是目前生产超高纯度钛的主要方法之一。其发展经历了传统碘化法和新碘化法两个阶段。传统碘化法的基本原理是把纯度较低的钛原料( 粗钛) 与碘一起充填于密闭容器中( 见图2) , 在一定温度下发生碘化反应, 生成TiI4, 再把TiI4通入加热的钛细丝上进行热分解反应, 析出高纯钛, 游离的碘再扩散
到碘化反应区, 继续进行反应。整个过程中发生了如下反应。
Ti( 粗) +2I2→TiI4( 200 ℃~400 ℃)
TiI4→Ti( 高纯度) +2I2( 1 300 ℃~1 500 ℃)
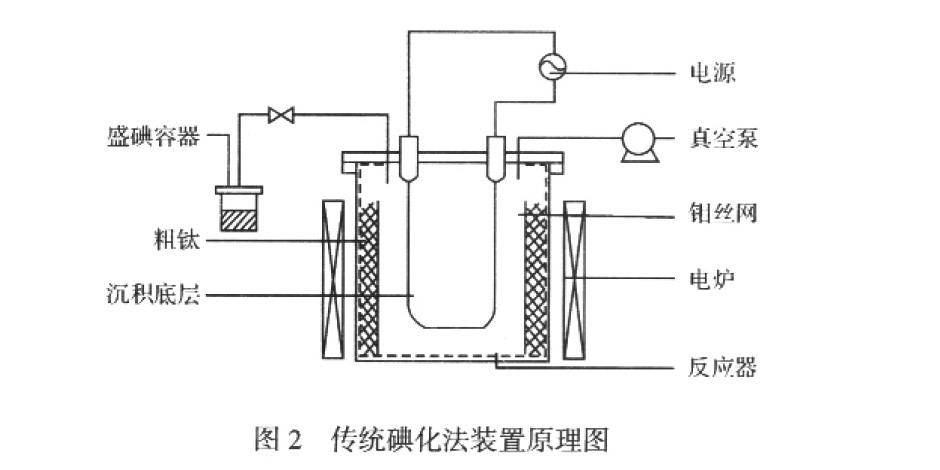
传统碘化法可以生产出高纯钛, 且在工业生产中有着重要的地位。目前国内生产纯度要求不是太高的高纯钛时采用此方法。但是, 传统碘化法尚存在如下问题: ① 反应在电热丝上进行, 容器盛放粗钛量有限, 反应速度慢, 生产效率低;② 由于是通电加热, 沉积层导致电加热丝电阻变化, 致使温度控制困难, 甚至导致加热丝熔断;③ 容易受到来自反应容器的污染。
为了解决传统碘化法存在的问题, 日本住友钛公司发明了一项新的碘化法。该方法可以生产出纯度达到6N 级的高纯钛。其基本原理是将气化的四碘化钛通入反应容器内把粗钛还原成低级的二碘化钛, 二碘化钛再在沉积表面被加热分解,同时除去过剩的碘化物, 使得反应连续进行, 最后析出高纯钛。图3 是新碘化法装置原理图。整个过程中发生的如下反应。
Ti( 粗) +TiI4→2TiI2( 700 ℃~900 ℃)
2TiI2→Ti( 高纯度) +TiI4( 1 100 ℃~1 300 ℃)
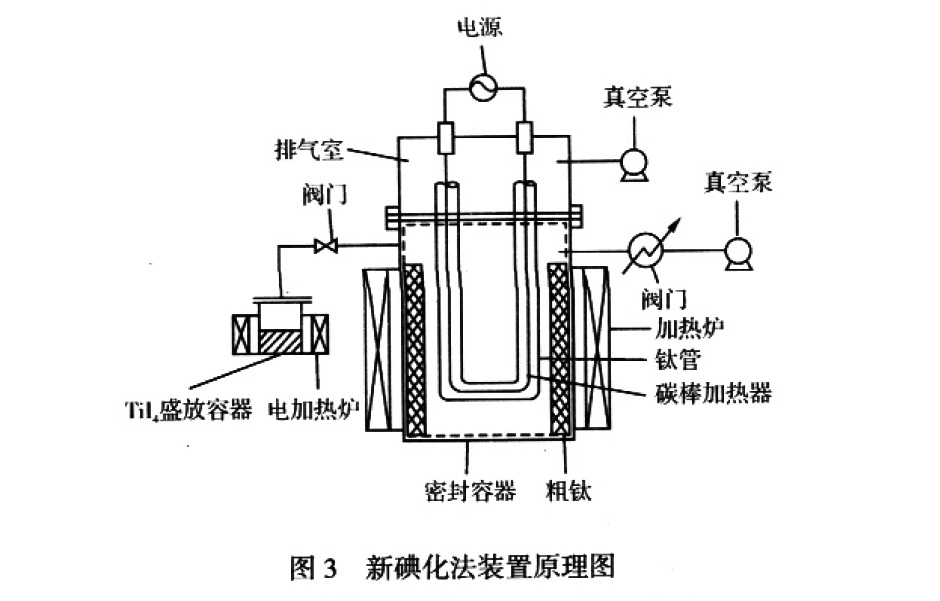
与传统碘化法相比, 新的碘化法降低了分解温度( 约200 ℃) , 使得工艺变得简单。此外, 新的碘化法还有以下优点: ① 以钛管代替了钛丝作为高纯钛的析出表面, 大大提高了生产效率; ② 采用间接加热方式, 不受沉积速度的影响, 有利于温度控制; ③ 粗钛压制成块, 容器可以放入更多钛原料; ④ 容器与反应气体接触的部分采用Au,Pt, Ta 镀层, 相比Mo 镀层具有更高的耐腐蚀性能和良好的抗破裂能力; ⑤ 减少了杂质元素的污染。
2.2 最新进展
近年来, 在提高碘化法生产效率等方面, 取得了一些新的进展。
美国冶金专家将碘化法的合成反应和分解反应分别在两个不同反应容器内进行, 大大提高了反应速度和生产效率, 同时减少了杂质元素的污染,制得的高纯钛杂质含量极低。R.F.K.Lam 等人从热力学角度系统地分析了碘化法制备高纯钛的基本原理, 并利用99.5%的粗钛生产出了99.999%的高纯钛。整个过程采用计算机监控与采样, 提高了生产效率。
中国专利也提供了一种利用碘化法生产高纯钛的装置和方法。该装置和方法具有分解沉积速度快、沉积表面积大、可形成较大的生产规模和能力、高温加热供电装置简单、加热过程容易获得恒温控制条件、产物与沉积部分容易剥离、获得的产品可直接用于加工无焊缝钛管等优点。
3、熔盐电解法
熔盐电解法是利用电化学原理制取纯钛的一种方法。该方法是以粗钛、钛合金或钛化合物作阳极, 在一定析出电位下使原料钛溶入电解液中, 并在阴极析出高纯钛。电解过程中溶出电位比钛高的杂质留在阳极上或沉淀在电解液中, 溶出电位比钛低的杂质也同钛一起溶入电解液中。熔盐电解法是发展比较早的一种方法。早在20 世纪60 年代, Freedman 等人就以78% K2TiF6与22% TiF4 的混合盐作为电解液, 以Ni 或Mo 为阴极, 粗钛为阳极, 制得了电解钛。为了找到电解法制取钛的最佳条件, E. Chassaing 等人研究了不同的熔盐对Ti 析出电位的影响, 发现不同的阳离子强烈地影响钛的析出电位。随后, L. P.Polyakova 等人[26~30]对NaCl + KCl + K2TiF6 熔盐系电解法的基本原理进行了详细研究, 并制取了高纯钛。Ervin 等人以TiC 为阳极, 以LiCl- KC1, NaCl-TiCl2, NaCl- K2TiF6 为电解液, 在密闭电解槽中,得到了电解粗钛晶体。近年来, 日本有学者采用高纯镍代替以往与熔盐接触的结构材料铁制备出了铁含量小于0.000 005%( 质量百分数) 的高纯钛。
此外, 山本仁通过改进电解槽结构来防止电极不纯物的溶出, 制取了纯度达到99.999%的高纯钛。
熔盐电解法采用的熔盐系虽有差异, 但目前主要以NaCl- LiCl- KC1 熔盐系为主。熔盐电解法制备高纯钛具有操作连续、成本低、除重金属杂质元素效果好等优点。但也存在熔体易污染、电解槽结构复杂、产量低等缺点。
总体而言, 采用熔盐电解法不易大规模制取高纯钛, 实际生产中熔盐电解法主要作为一种精炼方法, 即利用海绵钛作为阳极进行熔盐电解。
近年来, 虽然各国科学家想直接利用钛的化合物直接生产高纯钛, 但进展缓慢。文献介绍了几种利用熔盐电解法生产纯钛的方法, 但还不能大规模生产海绵钛, 更不能生产高纯钛。
4、电子束精炼法
电子束熔炼法是通过电子束加热, 使杂质元素蒸发, 或是通过熔融金属发生反应来达到提纯的目的。早些年, 由于熔炼装置复杂, 成本较高, 因而没有普及。近年来, 电子束熔炼又受到人们的关注。一般而言, 通过多次电子束熔炼可以不断提高金属的纯度, 这是制取超高纯钛的发展方向。
美国Honeywell International公司在电子束熔炼炉制造方面处于世界领先地位。利用该公司制造的300 kW 电子束熔炼炉目前能够生产出6N 级的超高纯钛。
归纳起来, 电子束熔炼方法的主要优点有:① 采用的是水冷铜坩埚, 因此与炉材的反应和污染少; ② 由于电子束易控制, 熔炼速度和能量可任意选择, 因此提纯效果相当好。缺点是除Fe,Ni, O 效果不佳, 而且重金属必须在电子束熔炼前用熔盐电解法或碘化法除去。
5、区域熔炼法
区域熔炼法是20世纪50年代为了提高半导体用金属的纯度而发展起来的一种金属提纯方法。其原理是利用杂质在金属凝固态和熔融态的溶解度差
别, 使杂质析出或改变其分布而得到高纯金属。基本操作过程是先在原材料一端建立熔区, 熔区由一端缓慢移向另一端, 使杂质元素分布在局部小区域内, 反复操作此过程, 可以得到纯度很高的金属,如提纯硅锗时可以达到8N 级( 99.999999%) 以上。
采用此方法生产高纯钛的最大优点是没有来自容器的污染, 缺点是生产效率低。相关资料表明, 目前西北有色金属研究院提供的普通高纯钛产品均采用此方法。图4和图5分别是区域熔炼设备示意图和区域熔炼法的原理图。
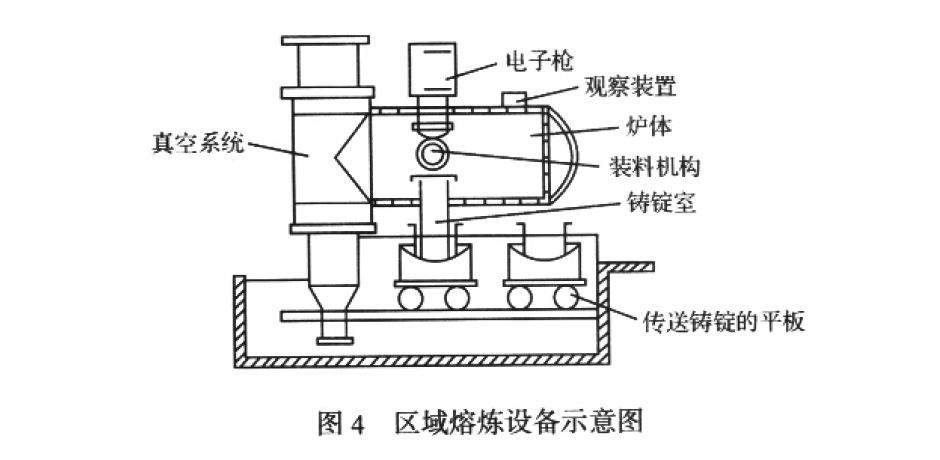
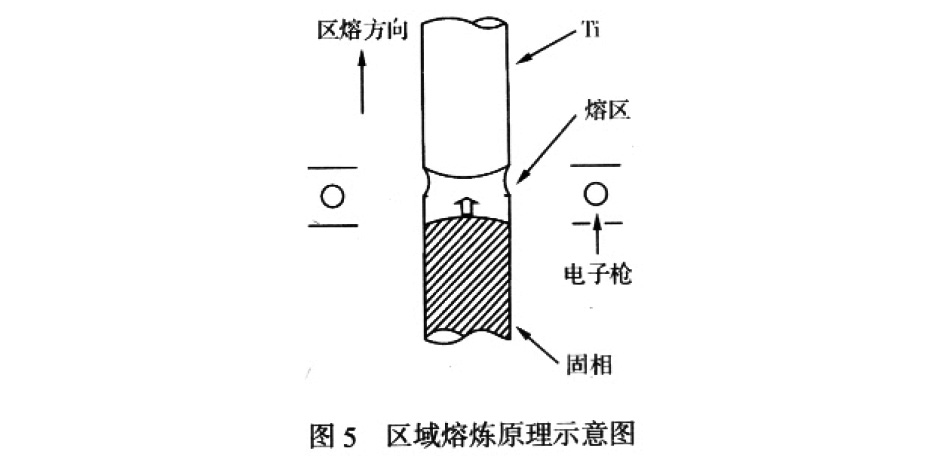
6、其他方法
离子迁移法和光激励精馏法是近年来发展起来的新方法。离子迁移法是利用间隙杂质元素的迁移率远大于构成晶格的金属原子的迁移率, 在超高真空或惰性气氛下, 将直流电通过棒状金属试样, 使金属处于炙热状态, 在外加电场的作用下引起金属晶格内杂质元素发生顺序迁移, 从而实现提纯的目的。该方法可以把O, N, H, C 含量降低到一个极低值。日本已利用离子迁移法把N, O 含量降至了0.01 w%, 美国达到了0.001w%。该方法的缺点是耗能大, 速度慢。光激励精炼法被认为是目前所有开发和待开发精炼技术中最先进的方法。基本原理是先利用电子束使真空室内的金属挥发, 再利用激光照射金属蒸气, 对金属进行选择性激励使其离子化, 并将它捕集分离在电极上, 从而达到提纯分离的目的。光激励精制法存在的主要问题是许多原子的激励离子化波长还不清楚。但是随着波长可调激光的出现, 为光激励精制法的发展创造了有利条件。
随着科学技术的进步, 生产金属钛的方法也在不断发展, 其中为了克服Kroll 法的成本高、不能连续化生产的缺点发展起来的一些方法, 如二氧化钛的直接电化学还原法、钙热还原法、ITP法、导电体介入反应法以及金属氢化物还原法, 得到了较大发展。但这些方法离工业生产还有很长的路要走, 目前也没有文献表明这些方法能够生产出纯度极高的高纯钛。
为了克服传统单一方法除去杂质元素种类有限和重复污染的问题, 采用联合方法和多阶段熔炼法可达到更好的除杂效果。联合方法应用较多的是熔盐电解- 电子束熔炼法、电子束熔炼-区域熔炼法、区域熔炼-高真空退火法等。熔盐电解-电子束熔炼法结合了熔盐电解法除Fe, Cr, Ni 元素容易和电子束熔炼法除K, Na 和气体元素容易的特点,可以制造出6N 级高纯钛。电子束熔炼-区域熔炼法可以除去大量气体杂质元素, 区域熔炼前进行电子束熔炼可以减少区域熔炼的次数, 提高生产效率。
区域熔炼- 高真空退火法可以进一步除去O, N 等气体元素。有资料表明, 采用集成的亨特法和熔盐电解法, 结合碘化法或电子束熔炼法可以生产出7N 级( 99.99999%) 超高纯钛。
今后, 高纯钛的制备将向两个方面发展: ①采用联合法和多阶段熔炼法制取高纯钛, 以克服传统单一方法除去杂质元素种类有限和重要污染的问题, 达到更好的除杂效果; ② 开发新的制备方法, 以克服老制备工艺的复杂性, 提高生产效率, 降低生产成本。
相关链接