钛合金比重小(约4.5)、熔点高(1600℃左右)、塑性好,具有比强度高、耐蚀性强,能在高温下长期工作(目前热强钛合金已用于500℃)等优点,因而已经越来越多地用作飞机和飞机发动机的重要承载部件,除了钛合金材料的锻件外,还有铸件、板材(如飞机蒙皮)、紧固件等等。现代国外飞机上采用钛合金的重量比已经达到30%左右,可见钛合金在航空工业上的应用有着广阔的前途。当然,钛合金也存在如下缺点:例如变形抗力大、导热性差、缺口敏感性较大(1.5左右)、显微组织的变化对机械性能影响较显著等,从而导致在冶炼、锻造加工和热处理时的复杂性。因此,采用无损检测技术以保证钛合金制品的冶金和加工质量,就是一个很重要的环节。
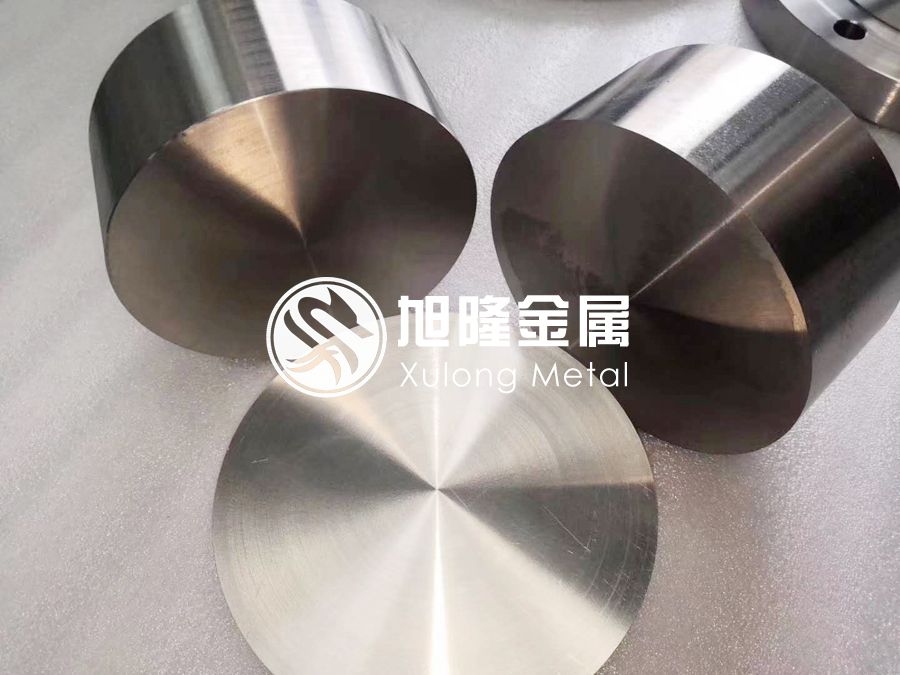
旭隆金属结合钛棒、钛环、钛管、钛锻件等产品的生产加工经验,结合相关资料,将钛合金锻件中容易出现的缺陷,整理如下:
1、偏析型缺陷
除了β偏析、β斑、富钛偏析及条状α偏析外,最危险的是间隙型α稳定偏析(I型α偏析),其周围常伴有细小的孔洞、裂纹,含有氧、氮等气体,脆性较大。还有富铝型α稳定偏析(II型α偏析),也因伴有裂纹并有脆性而构成危险性缺陷。
2、夹杂物
多是高熔点、高密度的金属夹杂物。由钛合金成分中高熔点、高密度元素未充分熔化留在基体中形成(例如钼夹杂),也有混在冶炼原材料(特别是回收材料)中的硬质合金刀具崩屑或不适当的电极焊接工艺(钛合金的冶炼一般采用真空自耗电极重熔法),例如钨极电弧焊,留下的高密度夹杂物,如钨夹杂,此外还有钛化物夹杂等。
夹杂物的存在容易导致裂纹的发生与扩展,因此是不允许存在的缺陷(例如苏联1977年的资料中规定,钛合金X射线照相检查时发现直径0.3~0.5mm的高密度夹杂物就必须予以记录)。
3、残余缩孔
1)Φ70mm钛合金锻棒中的残余缩孔
纵波(上为纵波波形照片)与横波(下为横波波形照片)均能发现,纵波探测时表现为强烈的缺陷回波并造成底波降低(面积型缺陷,可大致判断为径向走向),横波探测时表现为清晰强烈的缺陷回波(裂纹状缺陷)。右图为横向低倍照片(1x)。
2)钛合金饼坯中的钼夹杂(高密度夹杂物)
这是冶炼时作为铝钼中间合金中的钼未完全熔解而留在基体内形成,可用纵波探测到,无论改变超声频率及超声波束直径都能很好地发现,并且在两面探测时位置对应良好。解剖后验证为钼夹杂。在横向低倍上多呈“眼睛”状,在饼坯中的取向多与端面平行,但也有的会取向倾斜,在饼坯上不易发现,待模锻成盘形件后因变形力使其取向改变到与端面平行时才易于发现。左图为横向低倍照片(2x),右图为按超声束投射方向拍摄的X射线照片(外圈为铅丝,中间的白点即为高密度夹杂物-钼夹杂)
3)钛合金饼(环)坯中的45°裂纹及锻制板状件上的十字裂纹
这类裂纹是由锻造引起的,特别是从钛锭开坯锻制饼(环)坯时,往往因终端温度过低、锤击力过大等而沿最大变形应力方向开裂。这种裂纹大多在开口处弥合较紧,或者整条裂纹上的开隙度很不均匀,局部弥合很紧,经锻造后机械加工至半成品时,如果表面恰好在弥合较紧的部位处,则用腐蚀或渗透法有时未必能发现,但其内部开裂又较大,甚至出现孔洞(如照片b))。采用45°折射横波是很容易探测到并可以判断的。
4)Φ70mm钛合金轧棒上的径向表面裂纹
这类裂纹也属于锻造或轧制加工中形成的裂纹,可以用腐蚀或渗透法发现,采用45°折射横波作周面弦向扫查是很容易探测到的,而用一般的纵波周面径向入射探测是发现不了的。
5)Φ125mm钛合金锻棒的中心粗晶:用5P14直探头周面径向探测,中心部位的杂波水平(同声程比较)达到Φ1.2mm-6dB。
4、孔洞
孔洞不一定单个存在,也可能呈多个密集存在,会使低周疲劳裂纹扩展速度加快,造成提前疲劳破坏。
5、裂纹
主要指锻造裂纹。钛合金的粘性大,流动性差,加上导热性不好,因而在锻造变形过程中,由于表面摩擦力大,内部变形不均匀性明显以及内外温差大等,容易在锻件内部产生剪切带(应变线),严重时即导致开裂,其取向一般沿最大变形应力方向。
6、过热
钛合金的导热性较差,在热加工过程中除了加热不当造成锻件或原材料过热外,在锻造过程中还容易因为变形时的热效应造成过热,引起显微组织变化,产生过热魏氏组织。
相关链接