钛合金以其强度高、耐热性好、耐腐蚀性好、耐低温性好等特点,在航空、航天、石油、化工、机械、医疗等众多领域得到广泛的应用[1]。与其优异的物理特性相比,钛合金也属于典型的难加工材料, 因为其具有弹性模量小、导热系数低、化学活性强等缺点。所以在钛合金的加工过程中,常常伴随着切削温度过高,刀具磨损严重、变形系数小,单位面积切削强度大等加工特点。这些不利的加工特点势必会对钛合金工件的表面完整性造成一定的影响,进而影响钛合金的使用性能,所以在钛合金加工中表面完整性的控制成为了重要的研究课题。

国内外许多学者对钛合金加工过程中的表面完整性进行了有益的研究。Sun 和Guo[2]通过钛合金端铣试验研究了铣削参数对表面完整性的影响规律,发现铣削参数对表面完整性具有显著的影响。Yang 等[3]利用较低铣削速度和较高铣削速度分别对钛合金进行铣削试验,发现铣削速度的改变对表面完整性的影响较大。杨振朝等[4]在钛合金高速铣削试验中,基于有限元仿真技术研究了铣削速度对表面完整性的影响,发现铣削速度对切削温度和表面完整性影响显著。
Ribeiro 和Moreira 等[5]在钛合金的车削研究中发现,表面粗糙度随车削速度的增加而增加。Amin 和Ismail[6]在端铣钛合金时也发现了相似的规律。杨振朝等[7]在钛合金高速铣削试验的表面完整性研究中发现, 随着主轴转速的增加, 表面粗糙度先减小而后增加。
Brinksmeier[8]在金属切削试验的表面完整性研究中发现, 残余应力的分布深度及其数值大小受每齿进给量的影响较为显著, 且随每齿进给量的增加分布深度和数值大小均增加。Ginting 等[9]通过钛合金的端铣试验来研究切削参数对表面层显微硬度的影响规律, 将表面层显微硬度分为3 个区域来讨论, 论述了表面层显微硬度的形成原因。
在实际加工中, 影响表面完整性的因素比较复杂,包括切削参数、刀具几何角度、刀具磨损状态、冷却条件等。针对切削参数对表面完整性的影响来说,切削速度、进给量、切削宽度、切削深度对表面完整性的影响有所差别,然而目前对表面完整性的研究主要集中在讨论某一个切削参数对其的影响,比如仅仅研究切削速度对表面粗糙度的影响而没有兼顾研究其他切削参数(每齿进给量、切削深度、切削宽度等)的影响。同时,关于表面完整性中残余应力的研究主要为仿真研究,很少涉及到试验研究。这样对于全面地认识切削参数对表面完整性的影响规律及良好地进行表面完整性控制是明显不足的。
文中对Ti-6Al-4V(TC4)钛合金铣削过程中铣削参数对表面完整性(表面粗糙度、残余应力、显微硬度)的影响进行了充分地研究,分别分析了铣削参数(铣削速度、每齿进给量、铣削宽度、铣削深度)对表面粗糙度和残余应力的影响规律;同时,研究了不同的铣削速度、每齿进给量、铣削宽度条件下表面层深度与显微硬度之间的关系。为钛合金加工过程中设计合理的加工参数及良好地控制表面完整性提供了宝贵的试验数据基础。
1、表面完整性的定义及特征
早在1964 年,Field 等[10]首次确切提出表面完整性这个名词, 它是表征加工过程中零件表层材料产生各种变化的综合性指标,主要包括两个方面:(1)表面特征(表面波纹度、表面粗糙度、表面纹理方向和表面缺陷);(2)表层特性(残余应力、表层硬度梯度、微观组织变化)。同时,根据美国机械加工切削数据手册[11],表面完整性的评价准则主要包括最少数据组、标准数据组和扩展数据组这3 个级别标准。文中选用最少数据组作为钛合金铣削过程中表面完整性的评价标准。
2、试验规划
铣削试验的试件为TC4钛合金板材,其组成成分如表1所示,试件尺寸为长50mm、宽50mm、高35mm 的长方体, 试件材料在使用前经过普通退火处理并且通过时效处理以去除残余应力。试验在MazakNEXUS 410B-HS 型三坐标立式数控加工中心上完成, 刀具采用整体硬质合金4 齿平底立铣刀, 直径为20mm,前角12°,后角14°,螺旋角35°,铣削过程冷却方式采用乳化液冷却,铣削方式采用顺铣。

试验采用单因素的方法研究TC4侧铣过程中铣削参数(铣削速度v,每齿进给量fz,铣削宽度ae,铣削深度ap)对工件表面完整性(表面粗糙度,残余应力,显微硬度)的影响规律。侧铣试验中具体的铣削条件设计如表2所示,试验方案如图1所示。同时,在试验中为了保证试验结果的可靠性,表2中每组铣削参数均重复2次试验, 取其平均值作为最终的试验结果。
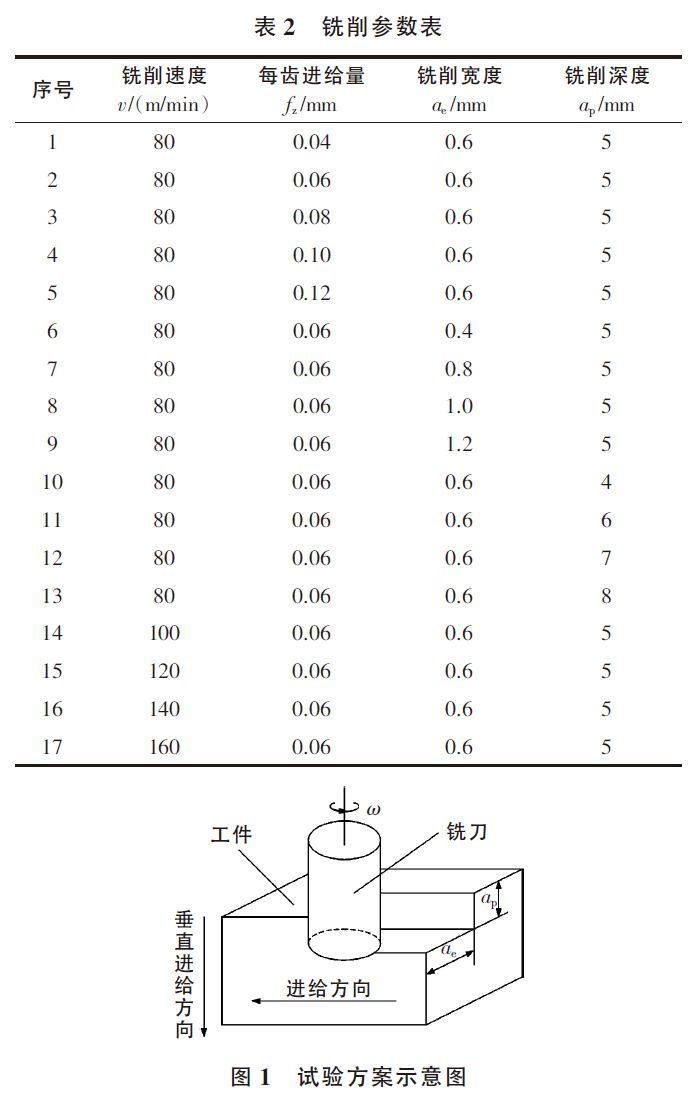
表面粗糙度的测量采用Talor-hobson PGI1250 型轮廓仪, 在测量过程中分别沿切削进给方向和垂直切削进给方向测量粗糙度值Rax和Ray。对每个加工表面的中心位置进行3 次测量, 其平均值作为最终的表面粗糙度结果,取样长度为0.8mm,评定长度为5.6mm。残余应力的检测使用X-350A 型残余应力仪,分别检测了同一表面上2个方向的残余应力(进给方向σx和垂直进给方向σy)。利用HVS-1000Z 型显微硬度计测量维氏显微硬度值, 显微硬度计的加载力为0.98 N,加载时间为10s,由已加工表面往下每隔20μm取一点进行测量, 直至所测的显微硬度值接近基体材料显微硬度为止, 测量中每个点均测量3次并取平均值。
3、试验结果分析
3.1 表面粗糙度
图2 为铣削参数对表面粗糙度影响的试验结果,从图2 中可以发现,在试验所在的铣削条件下,表面粗糙度随着铣削速度、每齿进给量、铣削宽度、铣削深度的增加而近似线性地增加,且进给方向的表面粗糙度Rax和垂直进给方向的表面粗糙度Ray的增长趋势一致。
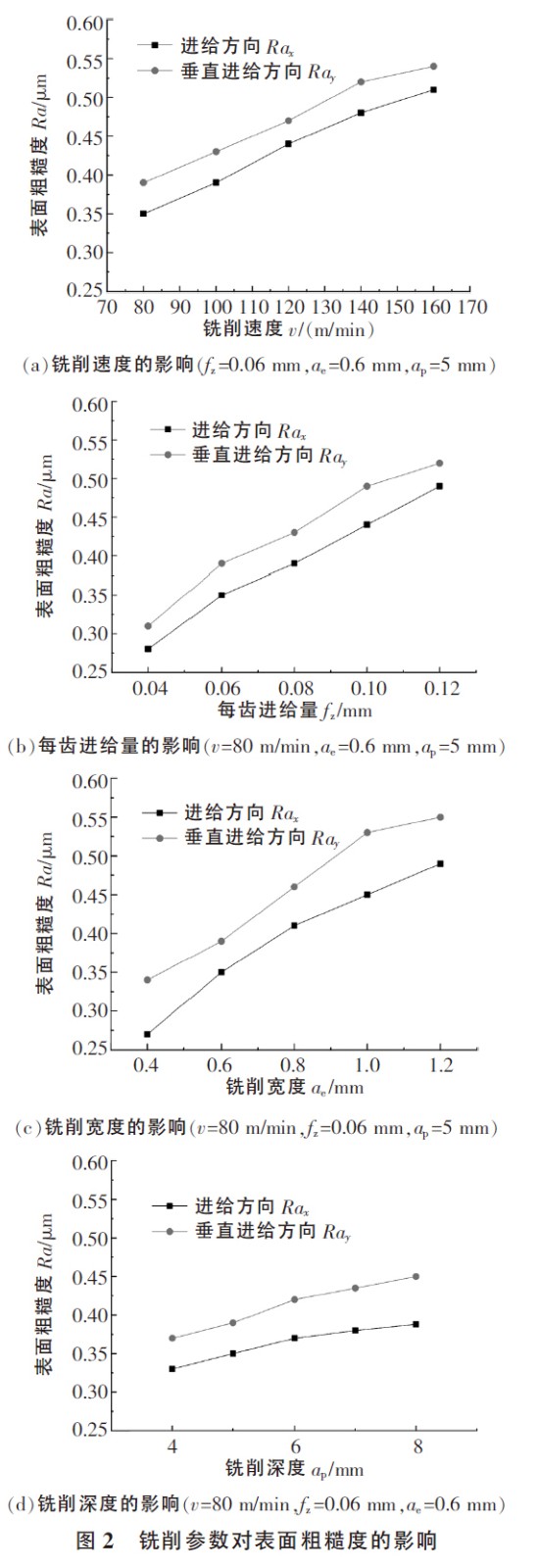
在图2a 中,铣削速度由80m/min 增加至160m/min时, 加工表面上2 个方向的粗糙度均随着铣削速度的增大而增加,其变化范围为0.35~0.54μm,表面粗糙度值由于铣削速度的影响增加了0.19μm。这是由于在加工钛合金时,随着铣削速度的增加,刀具磨损加剧,从而导致加工表面的表面粗糙度值增加。在图2b 中,每齿进给量由0.04mm增加至0.12mm, 使得铣削过程中铣削力随着每齿进给量的增加而增加, 从而导致表面粗糙度增加, 其变化范围为0.28~0.52μm。在图2c,d 中,随着铣削宽度和铣削深度的增加,使得铣削面积增加,铣削力成比例地增加,最终导致表面粗糙度增加。在试验所在的铣削宽度和铣削深度增加范围内,表面粗糙度的变化范围分别为0.27~0.55μm和0.33~0.45μm。
综合以上分析可以看出,随着铣削速度、每齿进给量、铣削宽度和铣削深度变化的影响,表面粗糙度值的变化范围分别为0.35~0.54μm,0.28~0.52μm,0.27~0.55μm,0.33~0.45μm。这说明铣削参数中各项参数对表面粗糙度具有不同的影响程度, 其中铣削宽度和每齿进给量对表面粗糙度的影响较大, 铣削速度的影响次之,铣削深度对表面粗糙度的影响较小。
3.2 残余应力
在加工过程中,弹塑性变形、热塑性变形和相变的综合作用产生了已加工表面层内的残余应力[14]。这些综合作用的形式主要包括刀具刃口前方区域的塑性凸出效应、后刀面与表层金属的挤光效应、加工过程的热效应和相变[15]。其中,挤光效应产生压应力,塑性凸出效应和热效应产生拉应力, 相变产生的残余应力状态取决于加工表面的体积变化方式。在一定的工况下,残余应力状态是压应力还是拉应力主要取决于以上哪些因素起主导作用[15]。
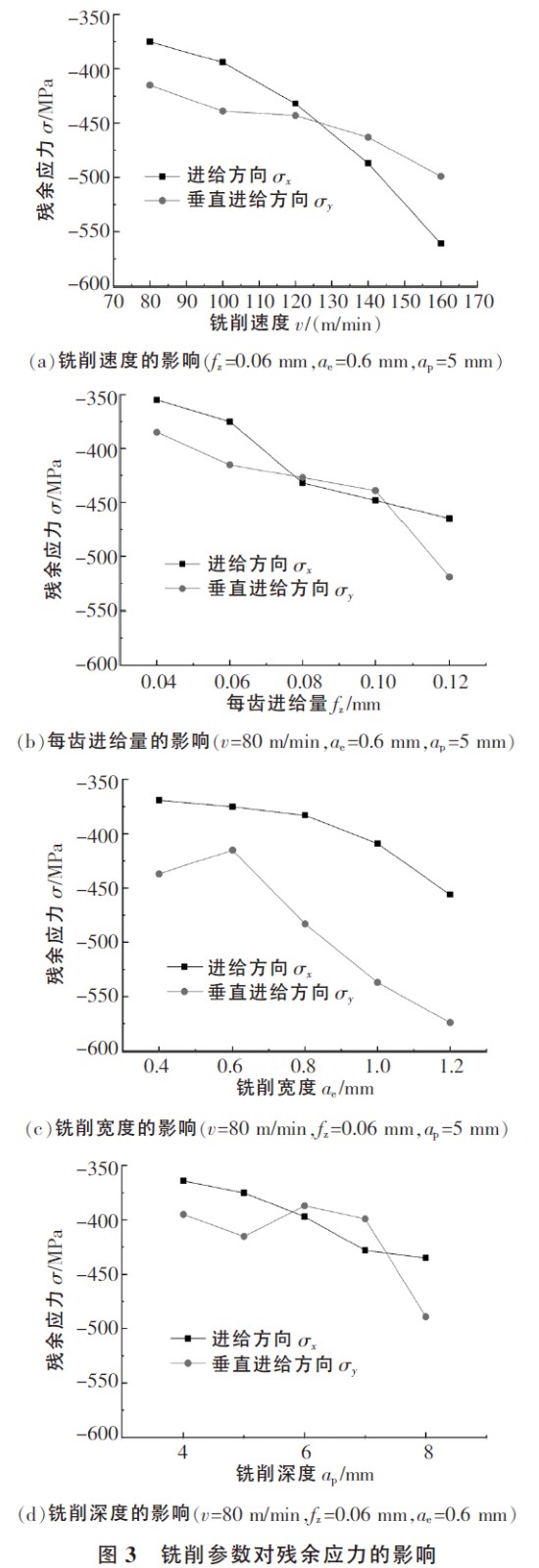
从图3 铣削参数对残余应力的影响可以看出,加工表面的残余应力均为压应力。这是因为:加工过程中产生的切削热大部分被切屑带走, 切削温度不高,表面层中的热效应较小,相变也没有发生;同时刀具始终处于初期和正常磨损阶段,铣削力较大,刀具和工件将会发生较严重的挤光效应, 此情况下挤光效应起主导作用。所以已加工表面的残余应力均
为压应力。
由图3a 可知,铣削速度从80m/min增至160m/min,进给方向的残余压应力σx和垂直进给方向的残余压应力σy均随着铣削速度的增加而增加,其变化的范围为375~561MPa;由图3b 可知,每齿进给量从0.04 mm增至0.12mm,2 个方向的残余压应力σx和σy均随着每齿进给量的增加而增加, 其变化范围为355~519MPa。这就说明随着铣削速度和每次进给量的增大,2个方向上的残余压应力σx和σy均具有增大的趋势。
这是由于铣削过程中随着铣削速度和每次进给量的增加,加工工件所需的铣削力加大,刀具与工件发生的挤光效应加剧,所以引起残余压应力增大。由图3c,d 可知,受试验误差和测量误差的影响,残余压应力σy出现了波动, 但是2 个方向的残余压应力σx和σy随着铣削宽度和铣削深度的增加总体上具有增大的趋势。
其具体增加形式为: 随着铣削宽度由0.4mm增至1.2mm,残余压应力的变化范围为369~574MPa;随着铣削深度由4mm增至8mm,残余压应力的变化范围为364~489MPa。这是因为铣削宽度和铣削深度的增加,最主要的作用是使得铣削面积增大,铣削力增大,加剧挤光效应,从而导致残余压应力增加。
3.3 显微硬度
图4 分别为不同铣削速度、每齿进给量、铣削宽度条件下,显微硬度随表面层深度变化的分布规律。从图4 中可以看出, 对于铣削速度、每齿进给量和铣削宽度,显微硬度随表面层深度变化的分布规律大体一致,即最大显微硬度值出现在已加工表面上, 而在很浅的表面层深度范围内显微硬度急剧下降, 下降至表面层深度h 为20μm处出现最小的显微硬度值,然后再次上升到高于基体显微硬度值, 并在h 为120~160 μm范围内出现稍低于已加工表面显微硬度的次峰值,紧接着呈下降的趋势,直至接近于基体的显微硬度值。
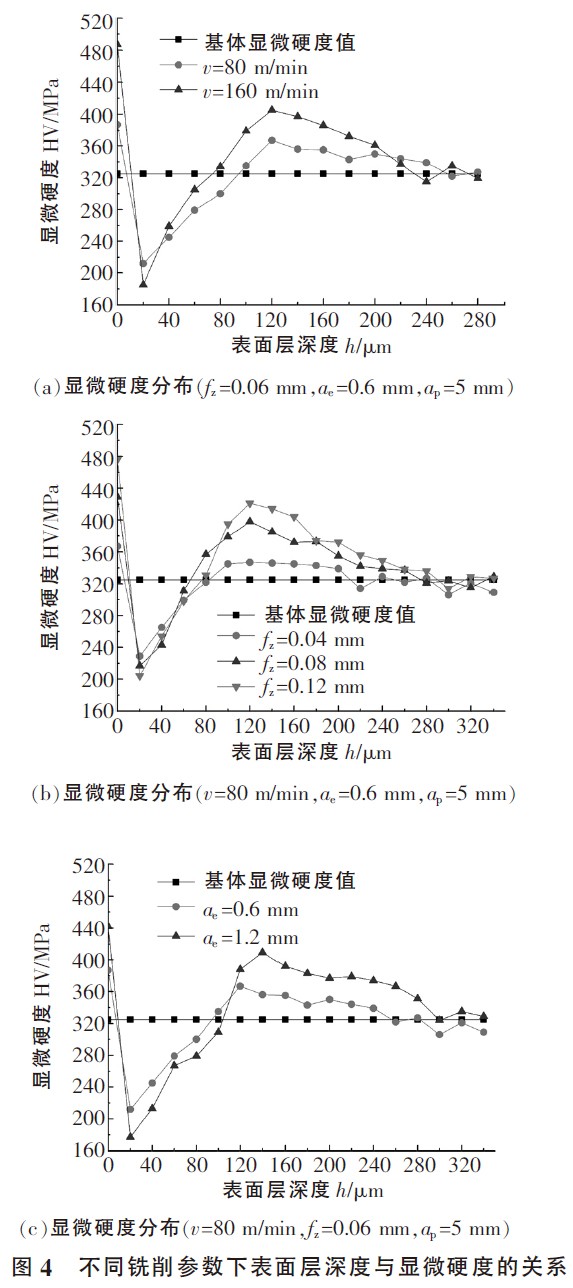
这是因为在钛合金加工过程中, 钛合金中的钛元素与空气中的氧元素和氮元素发生反应, 工件表面形成氧化钛和氮化钛薄膜,使工件脆性增加[16],进而使得已加工表面显微硬度最高。同时因为钛合金具有传热系数小,导热性差的特点,在铣削加工过程中产生的热量仅能传递到距离已加工表面很浅的深度范围内,并且主要集聚在h 为20μm处,所以h 为20μm处的材料被热软化而形成最小的显微硬度值, 然而由于钛合金铣削过程会产生应变硬化作用, 导致更深层材料受到挤压,引起深层材料的再次硬化,所以在有限的表面层深度范围内显微硬度随着表面层深度的增加而增加, 在应变硬化的作用下,h 为120~160μm范围内的表层金属出现显微硬度的次峰值(小于已加工表面的显微硬度),同时伴随着表面层深度的继续增加,材料受应变硬化的影响逐渐减弱, 所以显微硬度逐渐趋于基体显微硬度值325MPa。
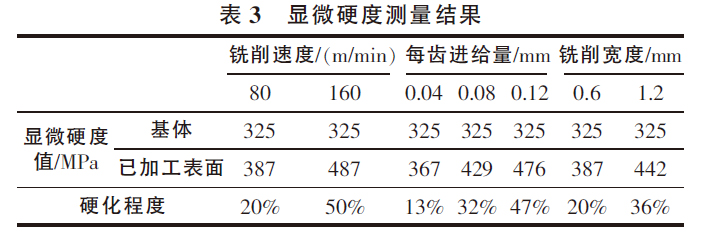
由图4 可知, 已加工表面的显微硬度相比于基体的显微硬度都有了明显的升高, 其相应的显微硬度值及硬化程度如表3 所示。从表3 中可以看到:已加工表面显微硬度值相比于基体增加了13%~50%;当铣削速度由80m/min升高至160m/min 时,已加工表面显微硬度由387MPa增加到487MPa; 每齿进给量由0.04mm 增至0.12mm时, 显微硬度由367MPa增至476MPa;铣削宽度由0.6mm增至1.2mm时,显微硬度由387MPa增至442MPa。这是因为随着试验中铣削速度、每齿进给量和铣削宽度的增加,钛合金中的钛元素与空气中的氧元素和氮元素所发生的反应也更加强烈,从而引起已加工表面上的显微硬度值也相应增加。
4、结论
通过对TC4钛合金铣削试验中表面完整性的研究,得到以下结论:
(1)在试验所在的铣削条件下,随着铣削速度、每齿进给量、铣削宽度和铣削深度的增加,表面粗糙度均具有增加的趋势; 铣削参数中各项参数对表面粗糙度的影响各不相同, 其中铣削宽度和每齿进给量对表面粗糙度的影响较大,铣削速度的影响次之,铣削深度对表面粗糙度的影响较小。
(2)进给方向的残余应力σx和垂直进给方向的残余应力σy均为压应力;总体上,随着铣削速度、每齿进给量、铣削宽度和铣削深度的增加,2个方向的残余应力σx和σy均具有增加的趋势。
(3)最大的显微硬度值出现在已加工表面上,已加工表面上的显微硬度较之基体增加了13%~50%;在表面层深度h 为20μm处,显微硬度值最小;随着铣削速度、每齿进给量和铣削宽度的增加,已加工表面上的显微硬度值也相应增加。
参考文献
[1] Chen G,Ren C Z,Yang X Y,et al. Finite element simulationof high speed machining of titanium alloy(Ti-6Al-4V) based on ductile failure model[J]. Int J Adv Manuf Technol,2011,56:1027-1038.
[2] Sun J,Guo Y B. A comprehensive experimental study on surface integrity by end milling Ti-6Al-4V[J]. Journal of Materials Processing Technology,2009,209:4036-4042.
[3] Yang X Y,Ren C Z,Wang Y,et al. Experimental study on surface integrity of Ti-6Al-4V in high speed side milling[J].Transactions of Tianjin University,2012,18(3):206-212.
[4] 杨振朝,张定华,姚倡锋,等. 高速铣削速度对TC4钛合金表面完整性影响机理[J]. 南京航空航天大学学报,2009,41(5):644-648.
[5] Ribeiro M V,Moreira M R V,Ferreira J R. Optimization of titanium alloy(Ti-6Al-4V) machining[J]. Journal of Materials Processing Technology,2003(143/144):458-463.
[6] Amin N A K M,Ismail A F,Khairusshima N M K. Effectiveness of uncoated WC-Co and PCD inserts in end milling of titanium alloy Ti-6Al-4V[J]. Journal of Materials Processing Technology,2007(192/193):147-158.
[7] 杨振朝,张定华,姚倡锋,等. TC4钛合金高速铣削参数对表面完整性的影响研究[J]. 西北工业大学学报,2009,27(4):538-543.
[8] Brinksmeier E. Residual stresses in hard metal cutting [J].Residual Stresses in Science Technology,1986(2):839-846.
[9] Ginting A,Nouari M. Surface integrity of dry machined titanium alloys[J]. International Journal of Machine Tools and Manufacture,2009,49:325-332.
[10] Field M,Kahles J F. The surface integrity of machined and ground high strength steels[J]. DMIC Report,1964,210:54-77.
[11] 美国可切削性数据中心. 机械加工切削数据手册[M]. 北京:机械工业出版社,1989.
[12] 曹春晓. 航空用钛合金的发展概况[J]. 航空科学技术,2005(4):3-6.
[13] 王桂生,田荣璋. 钛的应用技术[M]. 湖南:中南大学出版社,2007.
[14] 李友生,邓建新,张辉,等. 高速车削钛合金的硬质合金刀具磨损机理研究[J]. 摩擦学学报,2008,28(5):443-447.
[15] 杨晓勇,任成祖,陈光. 钛合金铣削刀具磨损对表面完整性影响研究[J]. 机械设计,2012,29(11):22-26.
[16] 张幼桢. 金属切削原理与刀具[M]. 北京:国防工业出版社,1990.
作者简介:李军(1990—),男,硕士研究生,研究方向:航空材料加工机理。E-mail:lijun168@tju.edu.cn
相关链接