钛及钛合金由于具有密度小、比强度高、耐腐蚀等优异性能,在航天航空、能源化工等领域广泛应用,然而在制造和使用过程中,钛板表面可能出现开裂、腐蚀等失效行为,严重影响其性能和使用寿命[1-2]。目前中国生产的钛产品表面缺陷较多,组织分布不够均匀,很大程度制约了钛规模化生产、高端化发展的前景,因此研究钛缺陷产生原因,对于改善钛产品质量具有重要意义[3-4]。
目前,国内研究者对钛合金板材表面开裂缺陷形成原因的研究主要集中在冶金因素和加工因素[5-9]。一方面国内部分采用真空自耗电子炉(VAR)方式生产纯钛及钛合金,高纯度钛产品即使进行2~3次VAR熔炼,依然无法有效去除低密度夹杂物、偏析等冶金缺陷,导致后续加工和使用过程中产生开裂,例如李渤渤等[10]指出VAR熔炼过程中中心疏松、气孔及硬α相引起冷轧纯钛分层开裂,杨柳[11]指出原始坯料中Al、Mo元素等杂质元素混入导致TA1纯钛冷轧薄板冲压开裂。另一方面不合理的加工工艺同样可以形成表面缺陷,例如张家铭[12]指出工业纯钛在冷轧过程中修磨位置底端的拉伸应力状态累积变形使材料产生开裂;黄德明等[13]指出当板材表面存在残留氧化层时,其与基体相比塑性较差,冷轧时沿轧向出现一系列小孔洞,随轧制进行产生大量条状裂纹;同时不合理的加工工艺使材料内部形成绝热剪切带,引起后续轧制过程中开裂[14-15]。
近期由VAR熔炼生产的纯钛冷轧薄板中部常出现规律性表面褶皱缺陷,严重的褶皱部位上可见不同程度的表面开裂,严重影响冷轧钛卷的成材率,现有文献对钢材中褶皱缺陷的分析和工艺优化较为成熟[16-20],但对TA1纯钛冷轧薄板生产过程中出现的褶皱及开裂缺陷进行表征与分析的研究较少。为明确表面开裂缺陷产生的原因以及与褶皱缺陷的内在联系,提高产品质量,本文有针对性地选取卷尾开裂部位及卷头褶皱部位进行微观表征分析,以达到研究冷轧板表面褶皱和轧制裂纹内在联系的目的。
1、试验材料及方法
1.1 试验材料
本试验采用的材料为TA1冷轧薄板,厚度为0.6mm,其生产工艺为:海绵钛—电极制备—VAR熔炼—锻造—热轧—退火—抛丸—酸洗—冷轧—退火—精整—包装;主要化学成分及其含量(质量分数,下同)为氧0.035%,氮0.03%,氢0.001 4%,其余为钛,符合国家标准GB/T 3620—2016要求。在多批次纯钛冷轧薄板成品包装检验过程中发现卷尾板宽中部存在部分表面开裂缺陷,且开裂位于严重褶皱缺陷区内,为进一步研究褶皱与开裂缺陷产生的原因,另取卷头板宽中部轻微褶皱缺陷区以作对比。
1.2 试验方法
截面金相采用硝酸、氢氟酸、水混合溶液(体积比为5∶2∶93)腐蚀,采用ZEISS Aix observer A5.m光学显微镜观察组织形貌,采用ZEISS Sigma500+INCA扫描电镜进行断口形貌及能谱成分分析,工作电压为20kV,工作距离为8.5mm;采用INNOVA TEST FAlCON 600硬度计对缺陷部位及正常基体部位进行显微硬度分析,载荷为500g,加载时间25s;正常部位及缺陷部位剪取薄片试样,经过化学抛光处理后,采用Leco-TCH-600氧氮氢分析仪平行测定氧、氮、氢含量3次,求平均值。
2、试验结果
2.1 宏观特征
图1为缺陷宏观形貌。尾薄板表面存在多处断续条状裂纹,裂纹分布于长度为100mm、宽度为7mm的褶皱条痕内,裂纹周围褶皱条痕扭曲、变形,无裂纹的褶皱条痕有明显凹凸感,条痕为或聚集、或独立排列的“川”字形貌,编号分别为1-1#、1-2#;卷头细小褶皱区长度为200mm,宽度为4mm,条痕独立整齐地排列形貌,上下表面光滑无明显凹凸感,编号为2#。
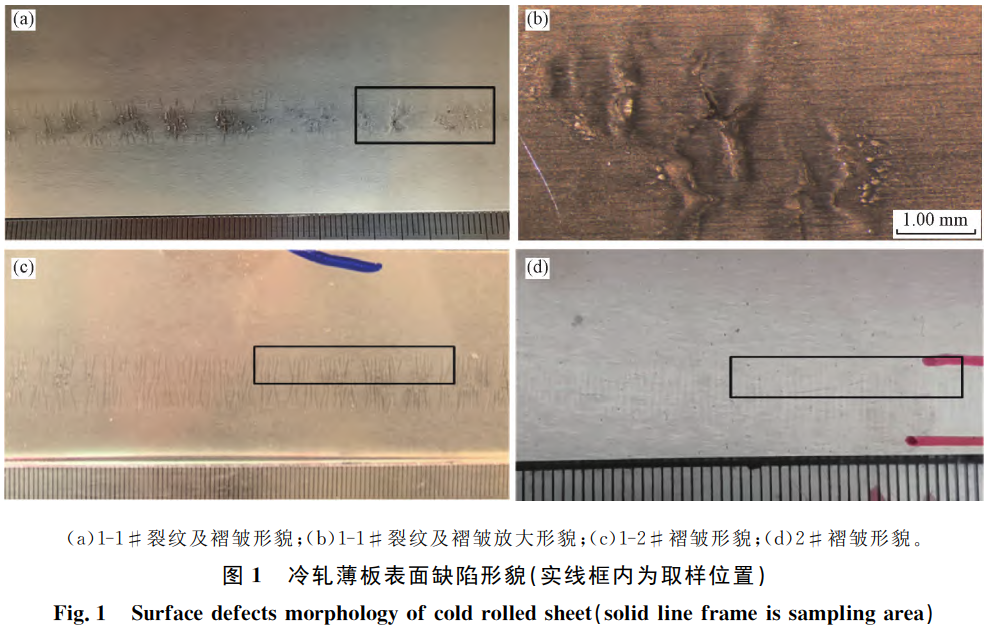
2.2 断口微观分析
图2为1-1#开裂样断口SEM形貌照片,电镜取样位置见图1(a)。表1和表2为试样断面能谱分析结果,图2(b)和图2(d)中黑色方框为各点能谱位置。切取断口试样时,断面自然脱落,开裂缺陷为穿透性表面裂纹,断面呈明显脆性断裂特征,可见多条二次裂纹,微观可见分层断面、颗粒状及河流状解理断面,扩展区及瞬断区均未见明显韧窝形貌,可见整个开裂断面已完全脆化,解理断面存在少量Al、O元素富集。
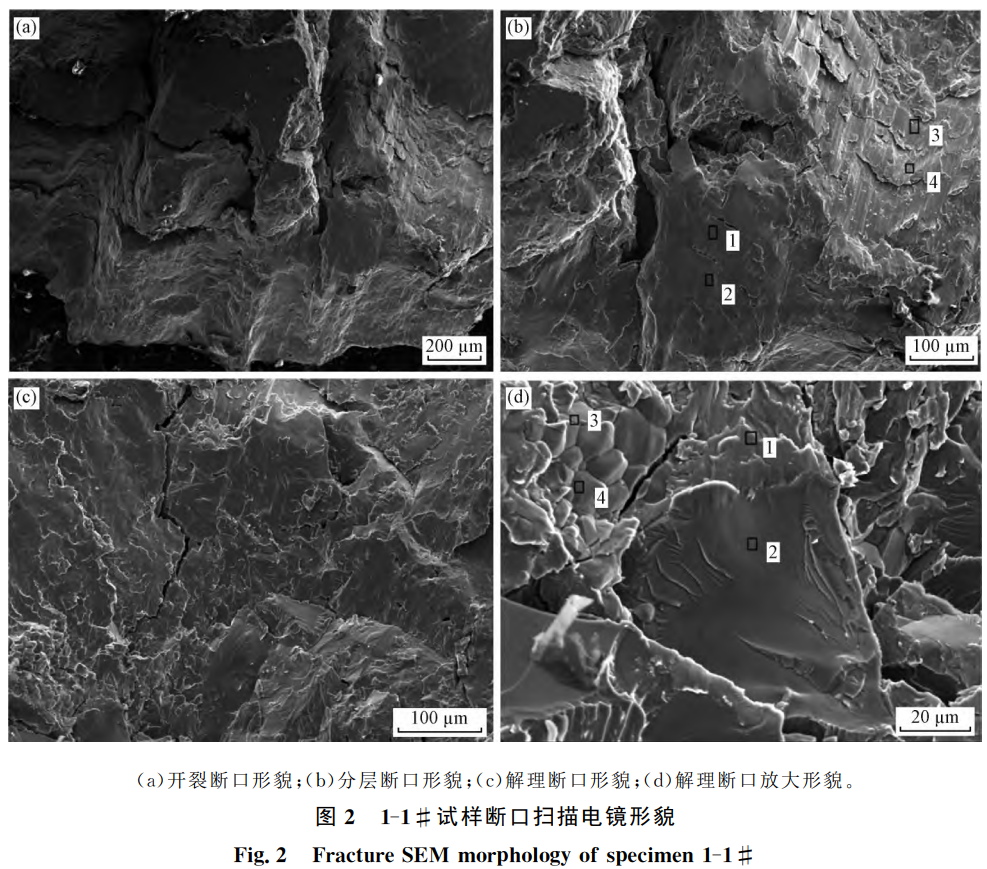
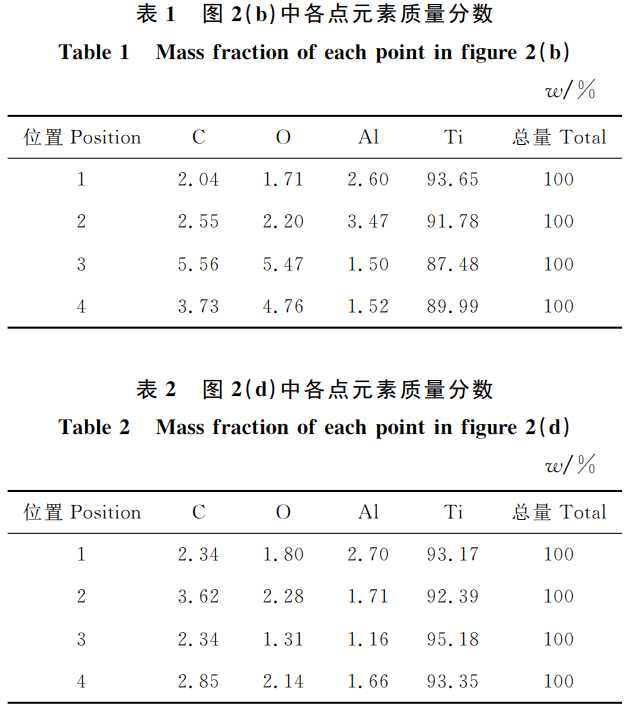
2.3 化学成分分析
表3为1-1#裂纹附近、1-2#褶皱区、2#褶皱区及基体的化学成分结果。1-1#裂纹附近O、N、H含量均远高于基体区,可见开裂后的退火过程严重增加了间隙元素含量,但开裂区存在异常的Al元素富集;1-2#氧元素含量为基体的2.9倍、2#氧元素含量为基体的1.9倍,N、H元素与基体一致,均未见同步增加,可见褶皱缺陷内部存在O元素富集现象,且O含量越高,褶皱条纹越明显。
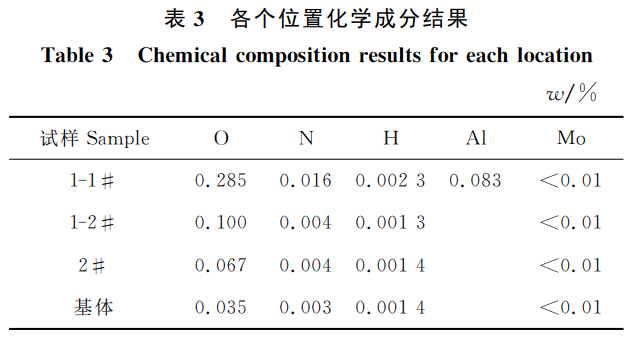
2.4 微观组织分析
图1(a)(c)(d)中黑色方框位置为金相取样示意图。图3为1#和2#试样金相组织形貌,腐蚀态可见基体均为等轴α相组织;1-1#开裂区组织为等轴+条带状α相,为典型未完全再结晶组织,且开裂缺陷为贯穿板厚的剪切裂纹,开裂处板厚为0.43mm,小于0.6mm的基板厚度,存在拉应力作用下的减薄现象,开裂区内可见多条沿条带α相扩展方向的二次裂纹,图3(a)箭头所示开口最大处可见圆弧形开裂形貌,该区存在与主开裂方式不同的弧线缺陷;1-2#褶皱区为未完全再结晶的等轴+条带状α相,且条带状α相的尺寸、含量均小于1-1#开裂区,心部为未贯穿板厚的尖角状内部裂纹,开裂高度为0.27mm;2#褶皱区为椭圆形的粗晶区,同样可见尖角状内部裂纹,粗晶区晶粒度为8.5级,细晶区晶粒度为10.0级,且裂纹形成于粗晶与细晶的交界处,开裂最大高度为0.064mm。
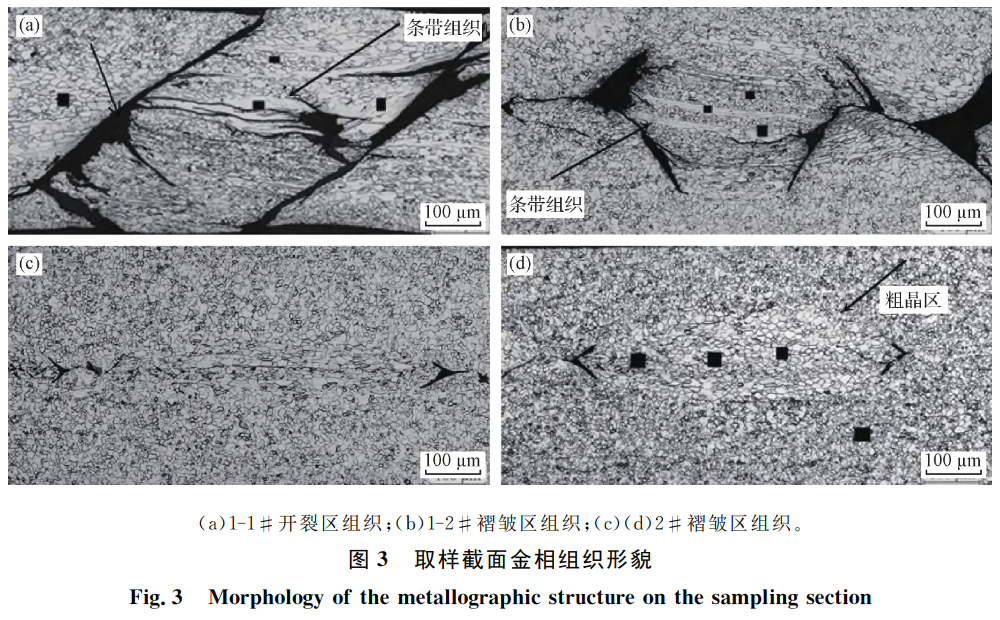
氧等杂质元素可显著提高材料开始再结晶温度,氧富集程度越大,开始再结晶温度越高,相同的退火温度下2#轻微褶皱区已形成等轴α相,1#褶皱区只能形成包含条带状α相的部分再结晶组织;褶皱首先沿氧富集区与基体的交界处起裂、扩展、连接,形成开裂程度不同的缺陷,包围的内部裂纹降低了板材的有效承载面积,在相同的轧制拉应力作用下形成剪切开裂,裂纹扩展方向与板材表面呈45°夹角。
2.5 显微硬度分析
表4为缺陷区显微硬度值,图3(a)(b)(d)中黑色方框为显微硬度测试位置。基体硬度为118.78HV0.5;1-1#开裂区平均硬度值为418.55HV0.5,是基体硬度值的3.52倍;1-2#褶皱区平均硬度为407.04HV0.5,是基体硬度值的3.43倍;2#褶皱区内平均硬度为378.75HV0.5,是基体硬度值的3.19倍;Al元素的增加不会显著提高材料硬度,因此1-1#显微硬度的增加应为元素的增加引起。
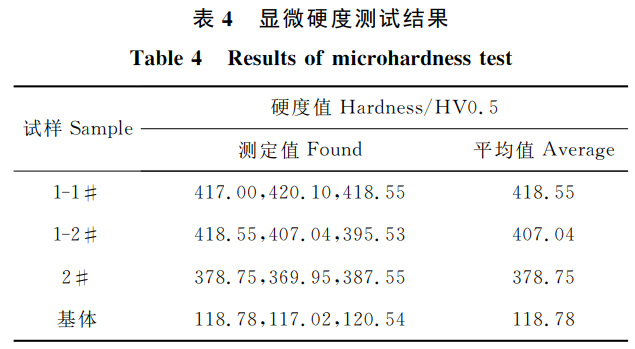
3、分析与讨论
缺陷内硬α相区内可见典型的条带状α相以及粗大α相组织,为不同的再结晶形态微观结构,条带状组织的存在可显著降低材料抵抗塑性变形能力,条带状组织形成原因主要有以下两个方面:(1)氧等杂质元素溶于基体后,趋向于位错、晶界处偏聚,阻碍位错的运动和晶界的迁移,同时杂质元素还阻碍了原子的扩散,显著提高其开始再结晶温度[21-22],在相同的退火温度下形成了基体与硬α区的不同再结晶组织;(2)形变计算模型(泰勒模型)认为[23],少部分的“白晶粒”再结晶发生在第二阶段,这些晶粒具有抵抗再结晶过程的位错结构,不会显著形核,再结晶过程被延迟,异常氧杂质元素的引入提高了开始再结晶温度,延长退火时间而退火温度没有进一步上升,这些晶粒将不会经历再结晶过程,变形组织将会保留下来形成异常条带状组织[24]。
表面褶皱与氧元素局部富集形成的硬α区有关,氧固溶于α相内,可显著提高该区显微硬度值;当褶皱区氧的质量分数为0.067%,平均显微硬度值为378.75HV0.5时,褶皱宽度为4mm;当氧质量分数为0.1%,平均显微硬度值为407.04HV0.5时,褶皱宽度为7mm;氧元素含量越高,硬度越大,褶皱缺陷越明显。随着冷轧过程的持续进行,板材厚度不断减少,变形较小的硬α区在厚度方向所含的分布含量逐渐增加,其变形时硬α区与基体区各晶粒变形不均匀,且各变形晶粒不能相互协调,保持α密排六方结构中的多个滑移系同时开动,降低了材料抵抗塑性变形的能力;当轧制拉应力超过材料承受极限时首先发生内部开裂,并逐步暴露出不同程度的褶皱缺陷,随着氧富集程度增加,热脆性Al元素的混入,硬度进一步增加,缺陷由内部开裂的褶皱缺陷扩展为宏观的开裂,形成穿透性的表面裂纹。
硬α区中氧元素的异常富集产生原因可能为氧化的海绵钛硬块,焊接电极时焊点严重氧化,也有可能是熔炼过程中真空度低、漏气率大产生的。Al元素富集产生的原因可能为海绵钛原材料或者熔炼环境污染,有文献表明[25]不当的补缩工艺会使挥发性Al元素在高温下进入缩孔等空洞处,并随着铸锭的冷却富集在空洞的表面,这样缩孔或空洞的表面可能形成Al等挥发性元素的富集,因此开裂缺陷处可见弧线硬α区表面富Al,导致在后续轧制过程中不能完全焊合形成一体,O、Al元素同时富集增加了材料的热脆倾向性,在断裂中形成脆性的解理断裂。
4、改进措施
(1)预防和减少表面褶皱的产生需尽量采用氧元素含量低的海绵钛,并在真空保护环境下焊接电极,减少原材料中氧元素的含量;预防和减少表面开裂缺陷的产生需严格控制原材料和熔炼环境中Al元素的混入。
(2)设计合理的热烘方案,确定合理的原材料干燥的温度、时间等参数,防止带有吸潮痕迹的海绵钛进入熔炼环节。
(3)加强熔炼过程控制,严格规范真空度、泄漏率、补缩时间和电流等,降低钛锭中氧的含量,促进Al杂质元素的挥发。
(4)增加钛锭低倍酸洗试验,确定合理的头尾切除量。
5、结语
(1)硬α区形成与原始铸锭中氧元素局部富集有关,氧等杂质元素的混入提高了材料开始再结晶温度,缺陷区出现了异常的未完全再结晶组织,硬脆等轴α相、条带状α相组织的存在严重降低了材料抵抗塑性变形的能力。
(2)表面开裂与褶皱均与板中心聚集的硬α区有关,硬、脆的α相在轧制过程中不能同步变形,首先形成内部开裂程度不同的表面褶皱,异常的杂质Al元素富集于部分硬α区加剧了材料脆化形成解理断裂,薄板由内部开裂的褶皱缺陷扩展为宏观的表面开裂。
(3)本文对褶皱表征及开裂原因进行了详细阐述,对纯钛冷轧薄板的开发研究起到参考作用,但缺乏对硬α区形成原因的直接证据,下一步将继续对生产涉及的各个工艺过程进行试验研究,以期获得不同环节形成硬α区的微观特征。
参考文献:
[1]李政,陈从喜.全球钛资源行业发展现状[J].地球学报,2021,42(2):245-250.
LI Zheng,CHEN Congxi.Development sTAtus of globAltiTAnium resources industry[J].AcTA Geoscientica Sini-ca,2021,42(2):245-250.
[2]邱冠周,郭宇峰.我国钛金属工业的现状及发展趋势[J].国际矿物杂志,2022,29(4):599-610.
QIU Guanzhou,GUO Yufeng.The present situation anddevelopment trend of tiTAnium metAl industry in China[J].InternationAl JournAl of MinerAls,2022,29(4):599-610.
[3]安仲生,陈岩,赵巍.2021年中国钛工业发展报告[J].钢铁钒钛,2022,43(4):1-9.
AN Zhongsheng,CHEN Yan,ZHAO Wei.Report onChina tiTAnium industry in 2021[J].Iron Steel Vanadi-um TiTAnium,2022,43(4):1-9.
[4]赵永庆.国内外钛合金研究的发展现状及趋势[J].中国材料进展,2010(5):1-8.
ZHAO Yongqing.Current situation and developmenttrendof tiTAnium Alloys[J].MateriAls China,2010(5):1-8.
[5]李明利,舒滢,冯毅江,等.我国钛及钛合金板带材应用现状分析[J].钛工业进展,2011,28(6):14-17.
LI Mingli,SHU Ying,FENG Yijiang,et Al.ApplicationsTAtus on domestic tiTAnium and tiTAnium Alloys plate andstrip[J].TiTAnium Industry Progress,2011,28(6):14-17.
[6]王瑞琴,黄先明,吴晓东,等.冷轧钛板材缺陷分析与讨论[J].热加工工艺,2014,43(13):147-149.
WANG Ruiqin,HUANG Xianming,WU Xiaodong,etAl.Discussions and ananysis of defects for cold rolled ti-TAnium sheet[J].Hot Working Technology,2014,43(13):147-149.
[7]何龙,张海龙,张延生,等.对钛及钛合金板材表面“酸斑”的探讨[J].钛工业进展,2005,22(5):41-43.
HE Long,ZHANG Hailong,ZHANG Yansheng,et Al.Discussion on“etching trace”on plate/sheet surface ofTi and Ti Alloy[J].TiTAnium Industry Progress,2005,22(5):41-43.
[8]付文杰,高维娜,蔡丹娜.轧制工艺对钛板质量的影响[J].热加工工艺,2015,44(19):137-139.
FU Wenjie,GAO Weina,CAIDanna.Effects of rollingtechnologies on quAlities of titianium plates[J].HotWorking Technology,2015,44(19):137-139.
[9]刘利香,马吉力,付振坡,等.开坯轧制钛板成材率影响因素及控制措施[J].宽厚板,2018,24(1):37-39.
LIU Lixiang,MA Jili,FU Zhenpo,et Al.Influencing fac-tors and control measures of yield ratio for tiTAnium platerolled from ingot[J].Wide and Heavy Plate,2018,24(1):37-39.
[10]李渤渤,陈涛,刘茵琪,等.冷轧纯钛带分层缺陷分析[J].材料开发与应用,2015,30(5):35-39.
LI Bobo,CHEN TAo,LIU Yinqi,et Al.AnAlysis on de-lamination defects of cold rolled tiTAnium strip[J].De-velopment and Application of MateriAls,2015,30(5):35-39.
[11]杨柳.TA1纯钛冷轧薄板冲压过程开裂原因分析[J].塑性工程学报,2018,25(2):73-78.
YANG Liu.AnAlysis on the causes of sTAmping crack-ing of TA1pure tiTAnium cold rolled sheet[J].JournAlof Plasticity Engineering,2018,25(2):73-78.
[12]张家铭,余伟,张泽宇.工业纯钛热轧及冷轧板表面缺陷研究[J].金属功能材料,2020,27(1):8-15.
ZHANG Jiaming,YU Wei,ZHANG Zeyu.Research onsurface defects of commerciAlly pure tiTAnium hot-rolledand cold-rolled plates[J].MetAllic FunctionAl Materi-Als,2020,27(1):8-15.
[13]黄德明,杨雄飞,韦青峰,等.TA17合金冷轧板材表面条状裂纹缺陷成因分析[J].钢铁钒钛,2013(1):26-30.
HUANG Deming,YANG Xiongfei,WEI Qingfeng,etAl.Cause anAlysis of strip cracks on surface of TA17Al-loy cold-rolled sheet[J].Iron Steel VanadiumTitanium,2013(1):26-30.
[14]付应乾,董新龙.工业纯钛动态压缩特性及破坏的实验研究[J].稀有金属材料与工程,2016,45(1):102-106.
FU Yingqian,DONG Xinlong.ExperimentAl studyonmechanicAl properties and failure characteristic of com-merciAlly pure tiTAnium under dynamic compre
ssion[J].Rare MetAl MateriAls and Engineering,2016,45(1):102-106.
[15]许峰,张喜燕,程佑铭.动态塑性变形纯钛的绝热剪切带研究[J].稀有金属材料与工程,2013,42(4):801-804.
XU Feng,ZHANG Xiyan,CHENG Youming.Study onadiabatic shear band in pure tiTAnium subjected to dy-namic plastic deformation[J].Rare MetAl Materials andEngineering,2013,42(4):801-804.
[16]刘英明,郭洪宇,关彬.连退机组炉内带钢褶皱缺陷控制[J].鞍钢技术,2017(4):51-54.
LIUYingming,GUO Hongyu,GUAN Bin.Control ofwrinkles defect on surface of strip steel heated in fur-nace of continunous anneAling mills[J].Angang Tech-nology,2017(4):51-54.
[17]张楠.低碳钢头部褶皱缺陷分析与预防措施[J].金属世界,2021(4):46-48.
ZHANG Nan.AnAlysis and preventive measurementsof low carbon steel head wrinkle[J].MetAl World,2021(4):46-48.
[18]刘昌明,刘斌,刘永前.热轧双相钢边部褶皱缺陷形成原因分析及改进[J].钢铁研究,2017,45(5):41-43.
LIU Changming,LIU Bin,LIU Yongqian.Cause anAly-sis of edge wrinkle forming of hot-rolled duAl-phasesteel and improving[J].Research on Iron and Steel,2017,45(5):41-43.
[19]彭进明,刘康康,柯鹏,等.椭圆孔型宽高比对线材表面变形状态的影响[J].物理测试,2021,39(3):13-17.
PENG Jinming,LIU Kangkang,KE Peng,et Al.Influ-ence of ovAl pass width-height ratio on surface deforma-tion of wire rod[J].Physics Examination and Testing,2021,39(3):13-17.
[20]张德松,杨霄,曹京华,等.方形轧件在椭圆孔的塑性失稳分析[J].物理测试,2020,38(1):31-35.
ZHANG Desong,YANG Xiao,CAO Jinghua,et Al.Plastic insTAbility anAlysis of square rolled parts in el-lipticAl holes[J].Physics Examination and Testing,2020,38(1):31-35.
[21]张翥,王群骄,莫畏.钛的金属学和热处理[M].北京:冶金工业出版社,2014:16-41.
[22]赵永庆,洪权,葛鹏.钛及钛合金金相图谱[M].长沙:中南大学出版社,2011:10-15.
[23]Tuomi T,Knuuttila L,Riikonen J,等.未掺杂VCz GaAs晶体的同步辐射X射线形貌[J].晶体生长学报,2002,237:350-355.
Tuomi T,Knuuttila L,Riikonen J,et Al.Synchrotron X-ray topography of undoped VCz GaAs crystAls[J].JournAl of CrystAl Growth,2002,237:350-355.
[24]刘娜.工业纯钛板材冷轧和退火过程中的微观组织及织构演变[D].重庆:重庆大学,2017.
[25]马宏声.钛及难熔金属真空熔炼[M].长沙:中南大学出版社,2010:160-167.
相关链接